In-Depth Analysis of Mechanical Modeling Software
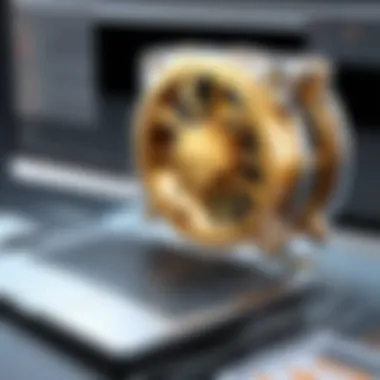

Intro
In today's fast-paced engineering landscape, mechanical modeling software serves as a fundamental tool in design, analysis, and simulation. It bridges the gap between conceptual ideas and practical applications, enabling engineers to visualize and optimize their designs before actual production. This article delves into the diverse array of software solutions available in the market. It aims to provide a detailed examination of their capabilities, while also considering key factors that influence the decision-making process within organizations.
Understanding the varied functionalities and distinguishing features of mechanical modeling software is crucial. Companies must navigate an increasingly complex software environment where usability, cost, and specific industry needs play a vital role. As we explore the current offerings, we will equip decision-makers with crucial insights, facilitating informed choices that align with their project requirements.
Overview of Key Features
Essential Software Capabilities
Mechanical modeling software encompasses a wide range of essential capabilities. Users seek tools that not only enable detailed modeling but also support simulation and analysis. Some key features include:
- 3D Modeling: Almost all tools allow users to create three-dimensional representations of their designs. This is central to visualizing the product before development.
- Simulation Functionality: This enables users to test their models under various conditions, predicting real-world performance.
- Finite Element Analysis (FEA): A crucial aspect for many engineers, FEA assists in identifying potential failure points of structures under stress.
- Compatibility and Integration: Ability to work with other software and systems is essential for seamless workflows.
Unique Features That Differentiate Options
Not all mechanical modeling software is created equal. Some products come with unique features that cater to specific needs or industries. For instance:
- SolidWorks: Renowned for its robust parametric modeling environment, which allows for design changes to propagate seamlessly across the model.
- Autodesk Fusion 360: Integrates engineering and design tools on one platform with cloud collaboration features, making it versatile for both individual users and teams.
- PTC Creo: Offers advanced capabilities like generative design, which optimizes designs based on real-world constraints and material use.
"Selecting the right mechanical modeling software can significantly impact the efficiency and outcome of a project."
User Experience
Interface and Usability
User experience is a crucial metric when evaluating mechanical modeling software. The interface must facilitate intuitive access to its myriad features. Tools like Rhino or CATIA have distinct interfaces that cater to specific user preferences. Companies often prioritize software that minimizes training time and accelerates project initiation.
Support and Community Resources
An established support system adds value to software products. Online communities, tutorials, and technical assistance can greatly enhance user experience. For example, software such as Siemens NX boasts an extensive user community where users can exchange insights and solutions. The availability of comprehensive documentation also simplifies the learning curve associated with new software adoption.
Prolusion to Mechanical Modeling Software
Mechanical modeling software plays a crucial role in modern engineering and design practices. As the complexity of projects increases, so does the necessity for software that can accurately simulate physical properties and behavior. This capacity is fundamental for predicting outcomes without the need for extensive physical prototyping, which can be both time-consuming and costly. Utilizing mechanical modeling software enables engineers and designers to visualize and modify their designs before actual production starts.
The primary benefits of mechanical modeling software include enhanced accuracy, improved efficiency, and the ability to explore innovative designs. With precise simulations, professionals can identify potential issues early in the design process, which significantly reduces the risk of failures after the production phase. Additionally, the ability to create virtual prototypes means that alterations can be made in real-time, streamlining workflows and optimizing resource allocation.
Moreover, it is essential to consider the specific elements that make mechanical modeling software effective. User-friendliness is one key criterion; software that is difficult to navigate can hinder productivity. Integration capabilities with existing tools and systems is another vital consideration, as companies often work with a range of software solutions. Lastly, cost analysis is crucial when selecting the right software. Businesses must weigh the functionalities and advantages against their budget constraints to make informed decisions.
In summary, understanding mechanical modeling software is indispensable for any organization involved in engineering, design, or manufacturing. Familiarity with its key offerings and considerations helps in selecting the most suitable tools to enhance overall productivity and innovation.
"The right mechanical modeling software not only saves time and resources but also elevates the potential for design innovation."
This article will delve deeper into these aspects, examining the significant role mechanical modeling software plays across various industries.
The Importance of Mechanical Modeling
Mechanical modeling is a cornerstone of advanced engineering design and analysis. It allows professionals to predict how mechanical systems will behave, which is crucial for optimizing performance and ensuring safety. Without mechanical modeling, the risks associated with design flaws can increase significantly.
One of the key benefits of mechanical modeling is its ability to streamline the design process. Engineers can explore various concepts and configurations without the need for physical prototypes. This results in substantial cost savings and reduced lead times.
Additionally, mechanical modeling enhances collaboration between teams. Engineers, designers, and manufacturers can work together more effectively when they have a shared set of data that accurately represents the physical properties and behaviors of a product. This leads to better communication and more integrated solutions.
"Mechanical modeling is not just a tool; it's an essential part of modern engineering that shapes every aspect of product development."
Applications in Various Industries
Mechanical modeling finds applications across various industries, providing tailored benefits that address unique challenges.
Automotive
In the automotive industry, mechanical modeling is vital for creating safer and more efficient vehicles. The models help to simulate crash tests and analyze vehicle dynamics, which contributes to improved safety features. AutoCAD, for instance, allows designers to create detailed drawings and simulations. The key characteristic of automotive applications is their focus on dynamic performance. Engineers can predict how vehicles will react under various conditions, which is why this area of mechanical modeling is especially valued. However, the complexity of the simulations can pose challenges in terms of software requirements.
Aerospace
The aerospace sector relies heavily on precise modeling due to the stringent safety requirements. Aerospace engineers use tools like ANSYS to model airflow and structural integrity of aircraft. A unique feature of aerospace modeling is its capacity for thermal analysis, helping to manage heat distribution during flight. This characteristic makes aircraft lighter and more efficient. On the downside, the costs associated with high-fidelity models can be prohibitive for smaller companies.
Manufacturing
In manufacturing, mechanical modeling aids in the design of machinery and the optimization of production processes. Using SolidWorks, engineers can create functional simulations of machines. The key aspect of this industry is its focus on efficiency and automation. The unique feature regarding manufacturing modeling is its ability to simulate production lines, allowing companies to identify bottlenecks before physical implementation. A potential disadvantage is the steep learning curve for complex software solutions, which may hinder new users.
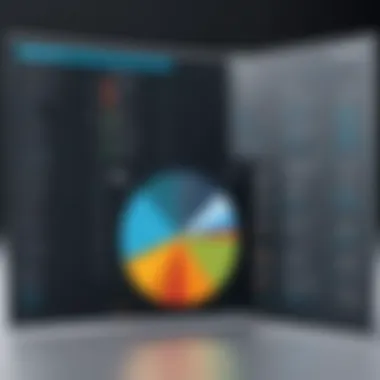

Consumer Electronics
The field of consumer electronics leverages mechanical modeling to refine devices such as smartphones and home appliances. These models can help ensure that products meet consumer demands for durability and aesthetics. The key characteristic here is the emphasis on user interaction, wherein designs are tested for usability and ergonomics. A unique feature of this application is the rapid prototyping phase that can take place virtualy, saving time before moving to physical prototypes. One challenge is the fast-paced nature of consumer technology development, pushing engineers to adapt models quickly.
Enhancing Design Efficiency
Mechanicla modeling plays a critical role in enhancing design efficiency across all industries. By allowing engineers to test concepts virtually, it reduces the iteration cycles required in traditional prototyping. As a result, products go from conception to market faster. Moreover, the use of advanced simulation tools provides insights that were previously difficult to obtain. With integrated solutions, the workflow becomes more organized, providing transparency for all stakeholders. This efficiency is invaluable for maintaining competitive advantage in rapidly evolving markets.
Key Features of Mechanical Modeling Software
The realm of mechanical modeling software encompasses a range of capabilities that cater to various engineering needs. Understanding these features is vital for professionals seeking to improve design, analysis, and troubleshooting processes. Key features play a significant role in ensuring compatibility with project requirements while maximizing efficiency.
User Interface Design
User interface design can significantly influence the productivity of engineers and designers. A well-structured interface allows for easy navigation and quick access to tools, making the overall experience smooth. An appealing layout can minimize the learning curve. Good user interface design integrates intuitive controls and visual cues, helping users to focus on their tasks rather than get hindered by complex commands.
Many leading software options prioritize usability and clarity, which is reflected in user feedback. Design tools that offer customizable layouts can enhance user satisfaction. While these enhancements can set a software apart, it is essential to balance aesthetics with functionality.
Simulation Capabilities
Static Analysis
Static analysis is critical for assessing the strength and stability of components. It analyzes how materials react under various forces without motion occurring. This feature is essential for validating designs before manufacturing. One key characteristic of static analysis is its ability to predict failure points under load. This predictive capability makes it a preferred choice in design validation processes.
However, static analysis has limitations. It cannot account for dynamic conditions and might oversimplify complex behaviors, which may be critical in certain applications.
Dynamics Modeling
Dynamics modeling addresses the behavior of systems in motion. It allows engineers to simulate real-world conditions and assess how systems will respond to changes. One of its key characteristics is its capacity to study the effects of forces and movements over time. This feature is vital for industries such as automotive and aerospace where performance is influenced by dynamic interactions.
Despite its advantages, dynamics modeling can be computationally intensive. Users may require significant resources to run complex simulations, which can be a drawback in time-sensitive environments.
Thermal Analysis
Thermal analysis evaluates how systems behave under varying thermal conditions. It is crucial for understanding heat transfer and temperature effects on materials. Key characteristics include the ability to simulate thermal loads and assess thermal stress. This capability is particularly important in areas like electronics cooling and materials development.
However, thermal analysis also presents challenges. Accuracy heavily depends on material properties, which may be difficult to obtain. Furthermore, integrating thermal analysis with other types of simulations can be complex, requiring advanced knowledge and tools.
Integration with Other Tools
Integration with other tools enhances the usability of mechanical modeling software. This feature ensures that users can streamline their processes, improving overall productivity. Integration allows for seamless data transfer between different platforms, enabling more comprehensive project management.
CAD Software
CAD software is integral for drafting detailed designs. Its connection with mechanical modeling software allows for direct updates between design and analysis. One key advantage is its ability to ensure that any changes in design are instantly reflected in simulations, reducing errors and miscommunications. This dynamic linkage is crucial for maintaining workflow efficiency.
However, compatibility between CAD and mechanical modeling software can sometimes be problematic. Disparities in file formats or versions can lead to data loss or conversion issues, increasing time spent on corrections.
Project Management Tools
Project management tools offer essential support in tracking project timelines and resource allocation. Their integration facilitates better coordination between multidisciplinary teams. One of the key characteristics is the way these tools enable team members to collaborate effectively through shared goals and milestones. This alignment is beneficial for achieving overall project efficiency and success.
Despite the advantages, the integration of project management tools can complicate workflows if not executed correctly. Poorly managed tool connections may create redundancy and communication gaps, undermining project objectives.
Understanding the key features within mechanical modeling software is critical. It empowers users to select the most suitable tools that align with their specific goals, enhancing productivity and effectiveness in their respective fields.
Types of Mechanical Modeling Software
Understanding the types of mechanical modeling software is essential for anyone involved in engineering, design, or simulation. Each type caters to specific functions and processes, allowing for more precise analysis and design. This section will delve into three major types: Finite Element Analysis (FEA), Computational Fluid Dynamics (CFD), and Multibody Dynamics (MBD). Knowing these types assists professionals in choosing the right tools that align with their project goals and methodologies.
Finite Element Analysis (FEA)
FEA is a crucial technique used for predicting how structures respond to various forces. It breaks down complex structures into smaller, manageable finite elements. Each element is analyzed under specific conditions, allowing for detailed insight into stress, strain, and deformation.
Benefits of FEA include:
- High accuracy in predicting structural responses
- Ability to model complex geometries
- Visualization of stress distribution
Applications of FEA range from automotive to aerospace industries, where safety and performance are paramount. Engineers use FEA software to refine designs before physical prototypes are made, thereby reducing time and costs.
Computational Fluid Dynamics (CFD)
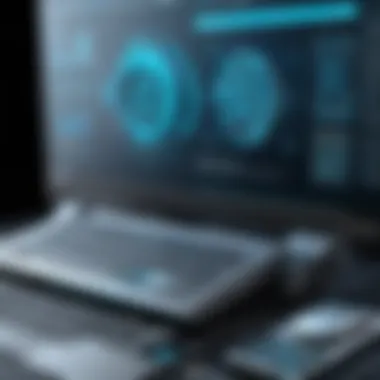

CFD focuses on fluid flow and its interaction with surfaces. This software enables engineers to analyze turbulence, heat transfer, and fluid interactions in a virtual environment. By using mathematical models, CFD provides insights that are difficult to obtain through traditional experiments.
Key advantages of CFD include:
- Ability to predict fluid behavior in various conditions
- Cost-effective simulation of airflow or water flow
- Insight into thermal dynamics
Industries like HVAC, automotive, and marine design extensively use CFD to enhance product performance. It allows engineers to optimize designs and solve potential issues early in the development process.
Multibody Dynamics (MBD)
MBD software simulates the motion of interconnected rigid or flexible bodies under the influence of forces and constraints. It is important for analyzing how different parts of a mechanical system interact over time. This simulation type helps in understanding complex interactions in machines, vehicles, and other systems.
Real-world applications of MBD include:
- Evaluation of mechanical systems such as Robotic arms
- Simulation of vehicle dynamics
- Assessment of kinematic behavior in assemblies
The MBD approach is vital in industries that require the integration of various components into a functional system. By utilizing MBD software, teams can achieve more reliable designs and fine-tune performance before physical testing.
"Selecting the appropriate type of mechanical modeling software is crucial for the success of any engineering project. It impacts accuracy, efficiency, and overall project outcomes."
Popular Mechanical Modeling Software Options
The choice of mechanical modeling software is crucial for engineers and designers. As technology progresses, the options available continue to evolve. This section will explore several prominent software solutions. Each option has unique strengths and functionalities that cater to specific needs in diverse industries. Recognizing these benefits is key for selecting appropriate tools that can enhance workflow and design precision.
AutoCAD
AutoCAD is one of the most recognized software in the engineering and architecture fields. It provides a versatile platform for creating 2D and 3D designs.
*
- Extensive library of pre-drawn objects helps users save time.
- Customization options allow users to create tailored toolsets.
AutoCAD's broad range of applications makes it suitable for various industries, including construction and manufacturing. Its user-friendly interface, however, can mask the complexity behind the scenes. For those new to the software, a steeper learning curve may present a challenge before fully utilizing its capabilities.
SolidWorks
SolidWorks stands out for its focus on 3D modeling. It employs parametric and direct modeling techniques that support intricate designs. This makes it a favored choice among product designers and mechanical engineers.
*
- Integrated simulation tools help to test designs under real-world conditions.
- Assembly analysis features allow users to visualize how parts interact.
Its robust community support offers numerous resources for users, enhancing the learning experience and providing assistance when needed. However, the cost may be a prohibitive factor for smaller companies or freelance professionals.
ANSYS
ANSYS is primarily recognized for its advanced simulation capabilities and engineering analysis tools. It provides extensive features for finite element analysis (FEA) and computational fluid dynamics (CFD).
*
- Commonly used for structural, thermal, and electromagnetic analyses.
- Integration with other engineering tools to improve workflow efficiency.
The software can handle complex simulations, making it valuable for industries that require high-precision calculations. While powerful, the intricate interface may be challenging for beginners, requiring considerable time investment to master.
MATLAB
MATLAB is not solely focused on mechanical modeling, but it provides significant benefits in numerical analysis, data visualization, and algorithm development. As a high-level programming language, it is particularly useful in simulations and computational tasks.
*
- Strong data manipulation capabilities.
- Extensive toolboxes available for various engineering applications.
MATLABβs diverse functionalities allow for customization and adaptability across different domains. However, its programming-centric nature might not appeal to engineers primarily focused on graphical modeling, which can lead to a steeper learning curve for those less familiar with coding.
Selecting the right mechanical modeling software is not trivial. It requires careful consideration of project needs, budgetary constraints, and user expertise. Assessing the unique features of each option can significantly impact project outcomes.
Considerations for Selecting Mechanical Modeling Software
Selecting the right mechanical modeling software is a crucial task for professionals in engineering and design. This decision directly affects project outcomes, design efficiency, and overall success. Therefore, the considerations during the selection process must be carefully evaluated to ensure alignment with organizational goals and specific project needs.
Budget Constraints
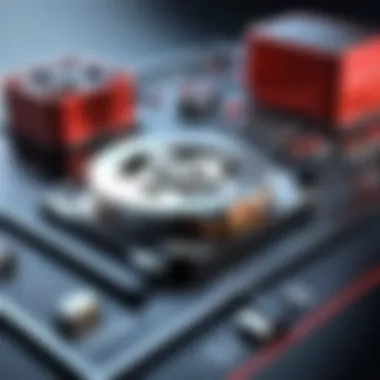

Budget constraints are often one of the primary limiting factors when selecting software. Investing in mechanical modeling software can require a significant financial commitment. Various options present different pricing tiers based on features, capabilities, and licensing structures.
- Initial Costs: The upfront cost of software can vary greatly. Some software like AutoCAD may have a straightforward licensing model, while others may incorporate additional hidden fees for updates or support.
- Long-term Value: Users should analyze the long-term benefits of the investment. A higher initial cost might offer a better return over time through efficiency gains and reduced labor costs.
- Total Cost of Ownership: This encompasses not just the purchase price, but also training, maintenance, and potential upgrades. Consider these factors to ensure that the chosen software provides sustainable value.
Skill Level of Users
The skill level of users is another critical consideration in the selection process. Understanding the proficiency of the team can dictate the suitability of certain software options.
- Training Requirements: Some sophisticated software, such as ANSYS, may necessitate extensive training. Teams with limited experience in such programs may face a steep learning curve, potentially delaying projects.
- Usability: User-friendly interfaces can greatly enhance productivity. Software that provides intuitive features can be easier for new users to master. Also, the learning resources available play an important role.
- Adaptability: The need to scale training based on user experience means selecting software that can cater to both novice and advanced users. This balance can maximize the effective use of the tools provided.
Support and Community Resources
Comprehensive support and community resources are vital for any software choice. They can significantly ease the implementation process and improve user satisfaction.
- Vendor Support: Evaluate the level of support offered by the software provider. Strong customer assistance can help resolve issues faster and reduce downtime.
- Community Engagement: An active user community is essential. Software like Solidworks often has forums and user groups where individuals can share insights or solutions to challenges they encounter.
- Learning Materials: Accessible tutorials, documentation, and webinars can enhance knowledge and reduce time spent troubleshooting. Well-documented resources make it easier for users to get started and master the software.
"Choosing the right mechanical modeling software hinges not just on preferences but also on financial, skill-related, and support-related considerations."
Challenges in Mechanical Modeling Software
Mechanical modeling software is integral to virtually any engineering discipline. However, the use of these tools does not come without its difficulties. Understanding these challenges is crucial for optimizing the modeling process and ensuring successful outcomes. This section delves into two key challenges: the complex learning curves and the inherent software limitations, both of which present significant barriers to effective utilization.
Complex Learning Curves
The initial encounter with mechanical modeling software often reveals a daunting reality: steep learning curves. Many of these tools, such as ANSYS or SolidWorks, boast intricate functionalities that can overwhelm new users. Unlike straightforward applications, mechanical modeling software encompasses a multitude of features designed for advanced simulations and precise modeling, which may necessitate extensive training.
Users often find it difficult to grasp the array of options available, leading to frustration.
"In the realm of mechanical modeling, proficiency can take significant time to achieve, often delaying project timelines."
Training programs vary in quality and depth; thus, organizations must invest in comprehensive educational resources to upskill their teams. As users become familiar with the interface and functionalities, they may still struggle with concepts like finite element method or computational fluid dynamics. It is imperative for companies to acknowledge this challenge and facilitate ongoing education while supporting teams through this initial journey.
Software Limitations
Even the most advanced mechanical modeling software has limitations. These restrictions range from computing power requirements to specific application constraints. Some popular tools may not support complex geometries or have predefined element types, which can restrict the modeling processes.
Additionally, interoperability issues frequently arise. Companies often use a combination of CAD and simulation software, yet compatibility is not always guaranteed.
- Data loss or corruption may occur if users try to convert files from one software to another without ensuring compatibility.
- Licensing restrictions can also limit users to specific features, reducing overall functionality based on their subscription choice.
Software developers continuously update and enhance their products; thus, existing users may face challenges keeping up. Embedded limitations can impede innovation and slow projects.
It is essential for professionals to assess these aspects before committing to a specific software tool, ensuring that their choice aligns with both immediate and long-term organizational goals.
Future Trends in Mechanical Modeling Software
The realm of mechanical modeling software is constantly evolving, driven by advancements in technology and changes in user needs. Understanding the future trends in this field is crucial for professionals who aim to remain competitive. These trends reflect not only the direction the software is heading but also the increasing integration of innovative technologies that enhance functionality and efficiency. As industries adopt more sophisticated simulation tools, it becomes important to recognize the elements shaping tomorrow's mechanical modeling landscape.
Artificial Intelligence Integration
The integration of artificial intelligence in mechanical modeling software has gained significant traction. AI technologies contribute to improving user experience and efficiency. Through machine learning algorithms, software can learn from user interactions and past design data. This empowers the software to suggest optimizations and corrections in real-time, facilitating faster decision-making. As a result, engineers can produce better designs with fewer iterations, minimizing time and resource expenditures.
Another benefit lies in predictive analysis. AI can analyze vast data sets to predict outcomes based on varying parameters. This capability is particularly useful in complex simulations, where analyzing countless possible scenarios manually is impractical. By leveraging AI, professionals can focus on creative problem-solving rather than being bogged down by the intricate details of computations.
"AI-driven tools are revolutionizing how engineers approach design and simulation, making complex tasks simpler and more efficient."
Cloud-Based Solutions
The shift toward cloud-based solutions is another significant trend in mechanical modeling software. By moving software to the cloud, organizations benefit from increased accessibility and scalability. Team members can access and collaborate on projects from any location, streamlining workflow and enhancing team collaboration. This is especially vital for businesses with remote staff or multiple locations.
Furthermore, cloud architectures often allow for better resource allocation. Users can run complex simulations on powerful cloud servers without needing extensive local hardware, reducing IT costs. Updates and new features can be deployed seamlessly in the cloud, ensuring users always have the latest tools at their disposal.
In addition, cloud-based solutions enable real-time data sharing and version control, minimizing errors during collaborative efforts. As industries evolve, adapting to these cloud ecosystems will prove advantageous for businesses striving for efficiency and innovation.
In summary, understanding these future trends is essential for professionals engaging with mechanical modeling software. With AI integration and cloud-based solutions on the rise, embracing these advancements can significantly improve productivity and innovation within engineering practices.
Closure
The conclusion serves as a critical element in this article, synthesizing the extensive discussions surrounding mechanical modeling software. It highlights how these tools are essential in various engineering fields, from automotive to aerospace design. Furthermore, it underscores the choosing of the right software as a strategic decision that can significantly affect project outcomes and overall success.
In summary, mechanical modeling software is not just a collection of functionalities but a significant investment. Decision-makers must consider not only the technical specifications but also how well these tools integrate with existing processes and workflows. A detailed understanding of software capabilities allows for informed decisions that ultimately improve design efficiency and reduce time to market.
Key elements to reflect on include:
- Understanding Specific Needs: Each industry and project will have unique requirements. Thorough knowledge of these can guide the choice of software.
- Usability and Training: The learning curve for these tools can be steep. Thus, ease of use, support, and available training resources should not be overlooked.
- Cost-Benefit Analysis: While budget constraints are a common concern, weighing the potential return on investment is essential to justify the costs involved.
- Future-Proofing: With rapid technological advancements, choosing software that seamlessly integrates AI or cloud-based functionalities can safeguard longevity and adaptability for future needs.
"The right mechanical modeling software can mean the difference between a successful project and costly delays."