Understanding Process Simulation Programs: A Comprehensive Exploration
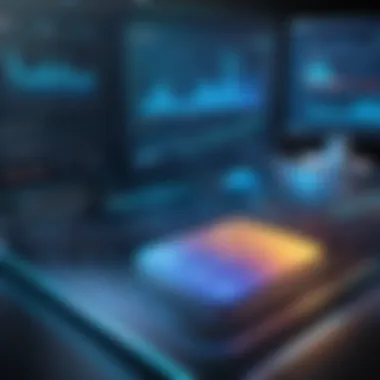
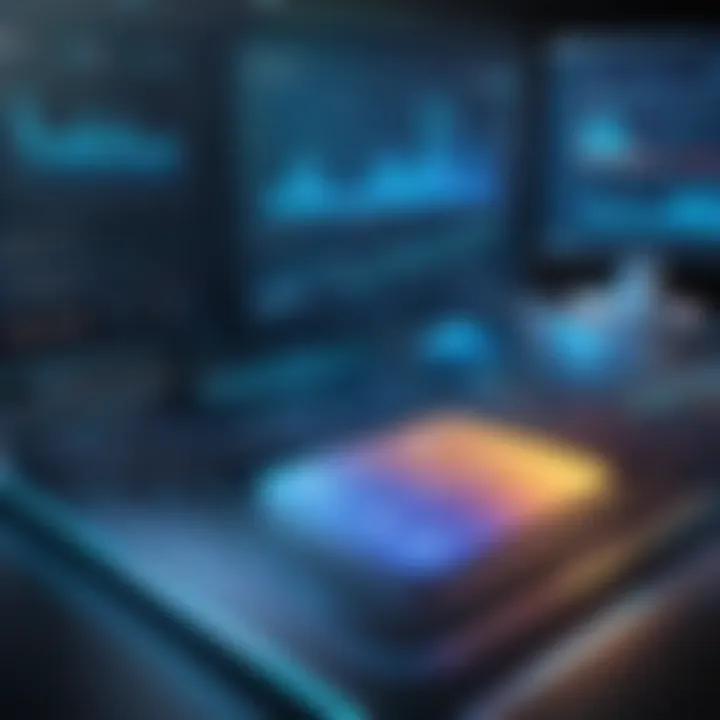
Intro
In today's fast-paced and data-driven environment, organizations across different industries are increasingly relying on process simulation programs. These advanced tools enable businesses to create accurate models of their workflows, which can lead to better analysis and optimization of operations. To truly grasp the significance of these programs, it is vital to explore their fundamental aspects. This exploration will ultimately aid in making informed decisions about the appropriate software solutions for various organizational needs.
Overview of Key Features
Process simulation programs are designed with a set of essential capabilities that streamline the modeling and analysis processes. Understanding these features can greatly assist in selecting the best software suited for specific applications.
Essential software capabilities
- Modeling: The capacity to create detailed representations of processes is crucial. This includes defining inputs, outputs, and the relationships between them.
- Simulation: The ability to simulate the behavior of processes over time, allowing users to visualize outcomes under various scenarios.
- Data Analysis: Integrated tools for analyzing data outputs help users assess performance, bottlenecks, and areas for improvement.
- Reporting: Comprehensive reporting functions provide insights through visual aids and detailed documentation, making findings accessible.
- Integration: Compatibility with existing systems enhances the software's utility, allowing seamless incorporation into workflows.
Unique features that differentiate options
Different process simulation programs offer unique features that can influence their effectiveness in particular contexts. For instance:
- Flexibility: Some programs allow for customization of the simulation environment, enabling users to tailor the model to specific business situations.
- User Accessibility: Certain programs focus on user-friendly interfaces, making them accessible to professionals with varying levels of technical expertise.
- Collaboration Tools: Advanced options offer collaborative features, ensuring that multiple stakeholders can engage with the model simultaneously.
User Experience
The user experience plays a vital role in determining the overall efficacy of process simulation software. Factors such as interface design and available support structures can significantly influence how effectively a user can operate the program.
Interface and usability
An intuitive interface is essential for promoting productive engagement with the software. Key considerations include:
- Navigation: Clear menus and shortcut options make it easier for users to access required functions.
- Customization: Users appreciate the ability to modify the workspace to fit their individual preferences.
- Feedback Mechanisms: Instant feedback on actions can guide users to make adjustments early in the modeling process.
Support and community resources
Having robust support options is critical for resolving user inquiries and issues. Notable resources include:
- Documentation: Comprehensive guides that cover both basic and advanced functions enhance understanding.
- Community Forums: Platforms such as reddit.com allow users to share tips and solve common challenges collectively.
- Customer Support: Reliable customer service options provide users with direct assistance when faced with more complex problems.
"Process simulation is not just a tool; it is a strategic partner that empowers organizations to refine their operations and advance their objectives."
As we proceed through this exploration of process simulation programs, the discussion will delve deeper into methodologies, applications, advantages, and limitations. By synthesizing this information, we aim to create a well-rounded viewpoint that can guide professionals in selecting optimal software solutions for their unique needs.
Preamble to Process Simulation Programs
The significance of process simulation programs cannot be overstated, particularly in today’s complex and fast-paced industries. These tools provide a structured approach to modeling, analyzing, and optimizing workflows. They are essential for businesses aiming to enhance productivity, improve decision-making, and minimize waste. Process simulation allows organizations to visualize and test various scenarios without impacting real-world operations.
Defining Process Simulation
Process simulation involves the creation of digital models that replicate physical systems or processes. This modeling can take numerous forms, including discrete event simulation, continuous simulation, or even hybrid methodologies. The primary goal is to understand how different elements within a process interact and how changes can influence outcomes.
The core components of process simulation include:
- Entities: These can represent customers, products, or resources in a system.
- Attributes: Specific properties associated with entities, such as size or delivery time.
- Events: Occurrences that affect the state of entities, like arrivals or departures.
- Attributes: These are measurable properties of entities, influencing the process.
- Resources: The assets required to execute the process, including machines, labor, or materials.
By simulating these components, users achieve insights into system behavior under varying conditions. This has broad applications across functions, from operations to finance.
Historical Context and Evolution
The evolution of process simulation can be traced back to early computer models developed in the mid-20th century. Initially utilized in engineering fields, the methodology gained traction as technology advanced, especially with the advent of faster and more robust computing capabilities.
- In the 1960s and 1970s, simulation became prominent in manufacturing sectors, enabling engineers to optimize production schedules and resource allocation.
- The 1980s saw the rise of software platforms like AnyLogic and Arena, which democratized access to simulation tools.
- Fast forward to the 21st century, process simulation has integrated with AI and big data, enhancing its predictive capabilities and flexibility.
Today, process simulation stands at the forefront of strategic decision-making. Organizations across sectors leverage it to not just assess current processes but to innovate and plan for future challenges.
Types of Process Simulation Programs
The importance of understanding the types of process simulation programs cannot be overstated. These different programs enable businesses and professionals to tailor simulations to their specific needs. Each type has unique features and is suited to particular kinds of problems. Knowing these distinctions helps users select the right tool for effective analysis.
Discrete Event Simulation
Discrete Event Simulation (DES) focuses on modeling systems where events occur at distinct points in time. In this context, each event triggers changes in the state of the system. DES is especially valuable in industries like logistics, manufacturing, and healthcare, where it can model complex interactions among resources, queues, and clients.
A key aspect of DES is its ability to provide insights into system performance metrics such as throughput, wait times, and resource utilization. Businesses can analyze scenarios such as changes in process flow or the introduction of automation. This aids in optimizing resource allocation and improving overall efficiency.
Considerations for using DES include:
- Complexity: Building a DES model can be intricate, depending on how detailed the simulation needs to be.
- Data Requirements: Accurate input data is necessary to ensure meaningful results.
- Validation: Testing and validating the model against real-world data is crucial for effectiveness.
Continuous Simulation
Continuous Simulation revolves around systems that change continuously over time. It uses mathematical equations to model the process, often represented in a time domain. Engineering fields, particularly those related to chemical processes or energy systems, often employ Continuous Simulation.
One significant advantage of Continuous Simulation is its efficiency in analyzing systems where time is a critical factor. This includes studying fluid dynamics or the behavior of chemical reactions in real time. Continuous models can show how gradual changes affect a system’s performance.
Key elements to consider with Continuous Simulation include:
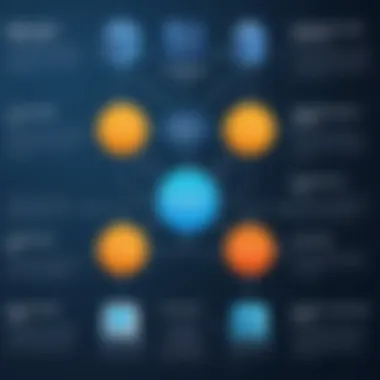
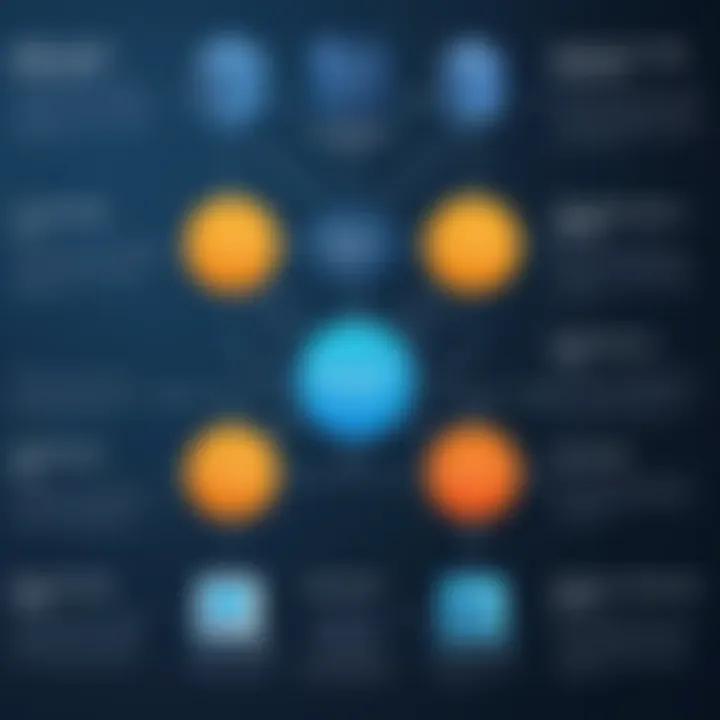
- Mathematical Modeling: Requires robust mathematical skills to create accurate representations.
- Computational Resources: Often computationally intensive, requiring significant processing power and memory.
- Real-time Analysis: Ideal for environments where real-time data analysis is essential.
Hybrid Simulation Approaches
Hybrid Simulation combines elements of both Discrete Event and Continuous Simulation to provide a more robust modeling framework. This type is particularly useful in complex systems where both discrete and continuous events interact. Industries like healthcare systems, where patients flow through various stages, benefiting from this approach.
By utilizing Hybrid Simulation, stakeholders can address scenarios that have mixed characteristics. For example, a supply chain might include elements of continuous flow (such as inventory levels) while also dealing with discrete events (such as order placements).
Advantages of Hybrid Simulation include:
- Flexibility: Can model complex systems more accurately by incorporating various dynamics.
- Comprehensive Insights: Offers a broader view of system interactions, leading to better decision-making.
- Resource Optimization: Helps in identifying optimal resource allocation strategies across different types of events.
In summary, recognizing these types of process simulation programs is essential for professionals aiming to enhance operational efficiency and effectiveness. The choice between Discrete Event Simulation, Continuous Simulation, or Hybrid approaches directly influences the insights gained and the decisions made.
"Choosing the right simulation type is paramount. Tailoring the simulation to fit the unique challenges can unlock significant efficiency gains."
Key Components of Process Simulation Programs
In the realm of process simulation, understanding the key components is vital. Each component plays a specific role in making simulation programs effective. Recognizing these ingredients allows users to optimize their workflows and make informed decisions. The key components include modeling elements, data integration and management, and simulation algorithms. Each of these components interacts with the others, creating a cohesive environment for simulating processes.
Modeling Elements
Modeling elements serve as the fundamental building blocks of any simulation program. These are constructs used to represent real-world processes in an abstract manner. Effective modeling allows for more accurate simulations, enabling users to replicate the behavior of complex systems. Common modeling elements include entities, resources, attributes, and events.
- Entities refer to the items or subjects being modeled, such as products in a manufacturing line or patients in a healthcare system.
- Resources are the tools or personnel required to process entities, like machines or staff members.
- Attributes are properties or characteristics associated with entities and resources, such as size or processing speed.
- Events mark changes in state or conditions within the simulation, triggering shifts in the process flow.
These modeling elements must be meticulously designed to reflect the actual system accurately. Poorly represented elements can lead to misconceptions in simulation results.
Data Integration and Management
In any simulation, data is the lifeblood that keeps the process dynamic and relevant. Data integration and management are critical for ensuring that the information feeding into the simulation is accurate and comprehensive. Efficient management of data allows for seamless operation and analysis.
A few important considerations include:
- Data Sources: Identifying reliable sources of data can significantly impact the simulation's effectiveness. Gathering data from various departments or systems increases the robustness of simulations.
- Data Quality: Ensuring that data is consistent, accurate, and up-to-date will improve results. Regular audits and quality checks are necessary aspects of data management.
- Data Flow: Proper organization and flow of data between systems prevent delays and errors during simulation. Integrating systems to facilitate real-time data exchange is a necessity in modern simulations.
In short, the integrity of simulation outputs hinges on the quality of data management strategies employed.
Simulation Algorithms
Simulation algorithms are the methods through which simulations run. These algorithms process the modeling elements and use the data to execute simulation scenarios. The choice of algorithm can significantly influence both the simulation's speed and accuracy.
Common types of simulation algorithms include:
- Discrete Event Simulation (DES): This method focuses on events that occur at discrete points in time. It is particularly useful for systems with defined state changes, such as queue management systems.
- Continuous Simulation (CS): In contrast, continuous simulation handles systems where changes happen smoothly over time, often seen in physical processes like chemical reactions.
- Hybrid Approaches: Some scenarios require the flexibility of both DES and CS. Hybrid simulations cater to complex systems that benefit from modeling both discrete and continuous elements.
It is crucial to select the appropriate algorithm based on the specific needs of the simulation and the characteristics of the processes being modeled. The right choice will enhance processing speed while ensuring that outcomes remain accurate and insightful.
"Simulation is invaluable for assessing potential outcomes without real-world repercussions."
In summary, the key components of process simulation programs—modeling elements, data integration and management, and simulation algorithms—harmonize to provide constructive insights. Understanding these components enables users to harness the full power of simulation, leading to better decision-making and process optimization.
Applications Across Industries
Understanding the applications of process simulation programs across various industries is crucial for grasping their real-world implications. These programs provide analytical frameworks that help organizations enhance efficiency and make informed decisions. From streamlining operations to assessing risks, their relevance spans multiple sectors. Incorporating process simulators allows companies not only to visualize workflows better but also to anticipate the effects of changes without disrupting actual processes.
Manufacturing Sector
In the manufacturing sector, process simulation plays a pivotal role in optimizing production lines. It allows manufacturers to create digital replicas of their physical processes. This helps in identifying bottlenecks, evaluating layout changes, and testing process modifications. Implementing simulation can lead to significant improvements in throughput and resource utilization.
For example, a car manufacturer may use simulation to analyze the assembly line's efficiency. By identifying delays or redundancies, the company can make data-driven adjustments. Such actions can potentially lead to reduced operational costs and enhanced product quality.
Healthcare Industry
The healthcare industry benefits considerably from process simulation programs as well. Hospitals and clinics utilize these tools for managing patient flow, staffing, and resource allocation. Simulations can analyze emergency response scenarios or scheduled surgeries, predicting wait times and optimizing staff assignments.
For instance, a hospital might use a simulation to test the impact of increasing patient volume on ER operations. The insights gained can help in determining necessary staffing levels and streamlining workflows, ultimately improving patient care and reducing costs.
Logistics and Supply Chain
Logistics and supply chain management rely heavily on process simulation to optimize logistics operations. By modeling different scenarios, companies can assess the impacts of various logistical strategies and supply chain configurations. This can involve analyzing distribution routes, inventory management, or supplier capabilities.
A leading retail brand might simulate the effects of changing shipping methods or distribution centers. The results would inform decisions that could lead to cost savings and improved delivery times. This kind of strategic planning is essential in today’s fast-paced market where customer expectations are high.
Energy and Utilities
In the energy and utilities sector, process simulation assists in the planning and operation of systems. Simulation programs can model energy production, distribution networks, and consumption patterns. This enables companies to anticipate demand fluctuations and optimize their operations accordingly.
For example, a power company may simulate its grid's response to variabilities in renewable energy sources like wind or solar. Such analysis can aid in developing strategies that ensure a stable power supply while maximizing the use of renewable resources. This integration leads to enhanced sustainability and operational reliability.
Process simulation programs are not just tools for analysis; they are integral to innovation and efficiency across industries.
Advantages of Using Process Simulation Programs
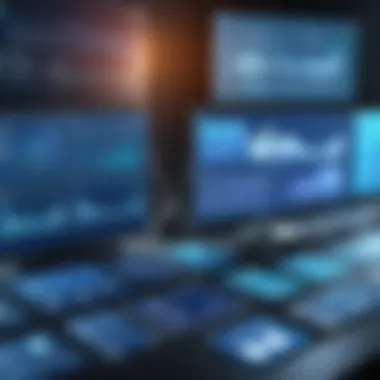
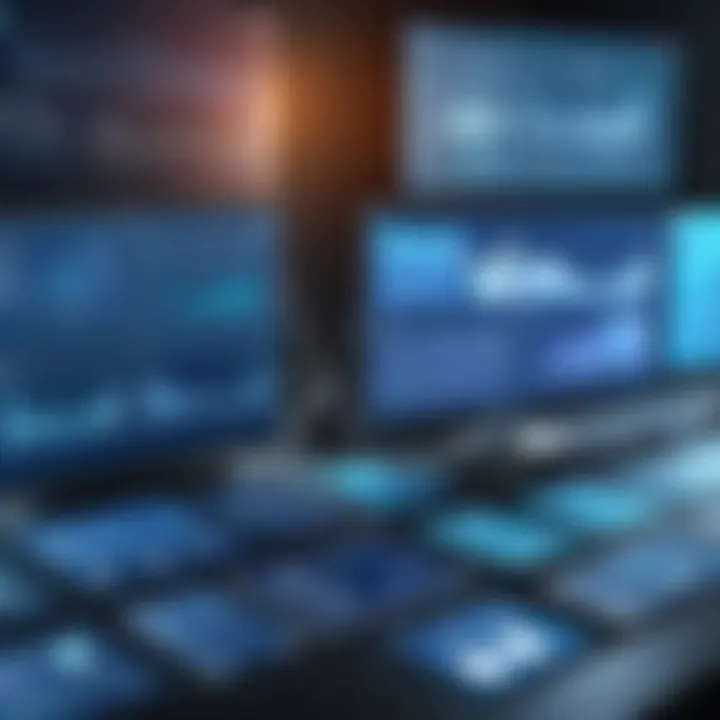
Process simulation programs offer significant benefits, making them essential tools in various industries. These advantages can significantly influence operational efficiency, strategic decision-making, and risk management. The ability to simulate different scenarios enables businesses to make well-informed decisions, optimize performance, and align resources strategically.
Enhanced Decision-Making
One of the primary advantages of process simulation is the improvement of decision-making. Organizations use these programs to analyze various workflows and processes before implementing changes. By simulating different scenarios, companies can evaluate potential outcomes based on various parameters without the risks associated with real-life implementation.
For instance, in the manufacturing sector, a company can simulate the production line efficiency under different conditions. This approach allows managers to visualize bottlenecks or inefficiencies and to test possible solutions. Such analysis leads to more informed decisions and can enhance overall performance.
In essence, process simulation acts as a predictive tool. It models the impacts of varying input factors, helping executives choose the most effective courses of action. This predictive capability is invaluable for strategic planning across domains.
Cost Reduction and Efficiency
Cost efficiency is another notable advantage. Process simulation helps identify unnecessary expenditures and resource allocation inefficiencies. By visualizing the workflow, organizations can optimize their operations, leading to material and labor cost savings.
Moreover, these programs allow for scenario testing without the costs associated with actual production changes. For instance, a logistics company can use simulation to determine optimal routing for deliveries, reducing transportation costs significantly.
Efficiency is also improved through better resource management. Process simulation allows organizations to allocate resources more effectively, responding quickly to changing demands and ensuring that all components of the process are operating at peak efficiency.
Risk Assessment and Management
Risk assessment is a crucial aspect of any organization. Process simulation programs provide a platform for identifying potential risks in workflows. By creating simulations of various scenarios, organizations can analyze the possible impacts of specific variables.
For example, in the energy sector, simulation can help assess the risk associated with fluctuations in energy demand. By understanding these risks in advance, businesses can develop strategies to mitigate their impacts, ensuring operational continuity even in adverse conditions.
Furthermore, process simulation can help prioritize risks based on their potential impact, allowing businesses to focus on managing the most critical issues. This systematic approach to risk management can enhance an organization’s resilience and stability.
In summary, process simulation programs not only enhance decision-making and reduce costs but also enable organizations to assess and manage risks effectively. These advantages combined contribute to a more robust operational strategy.
Limitations and Challenges
When discussing process simulation programs, it is essential to address the limitations and challenges that these tools present. Understanding these hurdles can guide professionals in their journey to implement these programs effectively. Limitations can take various forms, affecting the overall reliability and usability of the simulation software. Hence, it is crucial to engage with these challenges thoughtfully to optimize process simulation practices.
Accuracy and Validation Issues
One prominent challenge associated with process simulation programs is accuracy and validation. The output produced by these simulation tools is only as good as the models built and data inputs used. Often, discrepancies arise between simulated results and real-world outcomes. Factors such as imperfect data, assumptions made during model creation, and failure to account for dynamic changes in processes can lead to unreliable results.
Validating a simulation requires systematic testing against real processes. This task can be labor-intensive, often demanding a significant investment of time and resources. As a result, many users might skip the rigorous validation process, leading to misconceptions about the model's reliability. In industries where precision is paramount, such as healthcare and manufacturing, this issue becomes critical.
To make informed decisions, professionals must consistently assess accuracy and conduct thorough validations.
Complexity of Implementation
The complexity of implementing process simulation programs is another challenge that organizations face. Each software tool comes with its unique set of features, and some can be intricate to navigate. As organizations scale, integrating simulations into existing workflows can present significant integration hurdles. Teams often need to familiarize themselves with new software, requiring a steep learning curve.
Additionally, setting up the simulation environment can also be complex. It involves gathering inputs from various sources, creating accurate models, and defining parameters effectively. Misalignment within the team or a lack of technical skills can exacerbate these issues, leading to ineffective simulations. Moreover, the intricacies of modeling real-world processes accurately necessitate an ongoing commitment to refine models as conditions change over time.
Cost of Software and Resources
The cost associated with procuring and maintaining process simulation software can be a considerable barrier for many organizations. Licensing fees for advanced tools can vary greatly, and this does not account for the additional costs of the necessary hardware to run these programs efficiently. Organizations may find themselves scrambling for resources to support these tools, leading to budget constraints.
Furthermore, ongoing maintenance and upgrades are often required to ensure compliance with the latest technological advancements. This can entail not only financial resources but also the need for dedicated personnel who can manage these systems proficiently. Consequently, smaller organizations with limited budgets may find it challenging to rationalize such investments, thereby missing out on the potential benefits of simulation programs.
By understanding these limitations, businesses can better prepare for the realities of integrating process simulation into their operations. This can involve planning for proper validation strategies, investing in training, and ensuring a comprehensive approach to budgeting and resource allocation. Only then can the true value of process simulation programs be realized across various industries.
Best Practices for Implementation
Implementing process simulation programs requires a structured approach. Best practices serve as essential guidelines to ensure success in deployment. Utilization of these practices not only enhances the efficiency of the simulation process but also maximizes return on investment. Furthermore, adherence to best practices mitigates common pitfalls faced during implementation.
Identifying Objectives and Goals
Defining clear objectives and goals is the first step in the implementation of process simulation programs. Without a precise understanding of what an organization wishes to achieve, it becomes difficult to assess the performance or results of the simulation. Goals could range from reducing operational costs to improving production efficiency. For instance, a manufacturer might aim to decrease material wastage by 20% through more calculated process flows.
This phase includes:
- Stakeholder Involvement: Gathering input from all relevant parties ensures that their perspectives and needs are considered.
- Goal Clarity: Clearly articulated goals should be measurable and time-bound. This helps in tracking progress and making necessary adjustments.
Identifying objectives in the early stages significantly influences the implementation trajectory. It aligns the simulation design with the strategic vision of the business.
Selecting Appropriate Software
Choosing the right simulation software is paramount for the success of any process simulation project. The selected software must align with the outlined goals and accommodate the specific needs of the organization. Factors to consider include:
- Functionality: Does the software provide the necessary features, such as discrete event simulation or continuous process modeling?
- Interoperability: The software should integrate seamlessly with existing systems and data management tools. For example, software like Anylogic or Simul8 has various capabilities that may be beneficial based on the organization's requirements.
- Scalability: As businesses grow, their needs evolve. The chosen program should be able to scale accordingly. Grasping the long-term requirements is essential when making this selection.
Training and Knowledge Transfer
Training employees on using simulation programs is crucial for ensuring that the tools are utilized to their full potential. Effective training incorporates:
- Hands-on Learning: Interactive sessions allow users to engage with the software actively. This boosts confidence and familiarity with the program's interface and functionalities.
- Continuous Education: Technology and processes evolve. Ongoing training ensures that users stay updated on new features and methodologies introduced in the software.
- Knowledge Transfer: Experienced users should mentor newer participants. This framework benefits the organization as it preserves institutional knowledge and elevates the overall competency level of the team.
"The successful implementation of simulation programs hinges on clarity in objectives, the right software choice, and comprehensive user training."
Implementing these best practices helps organizations to optimize their process simulation efforts effectively. Following these guidelines allows for better planning, execution, and ultimately, achievement of desired outcomes.
Case Studies in Process Simulation
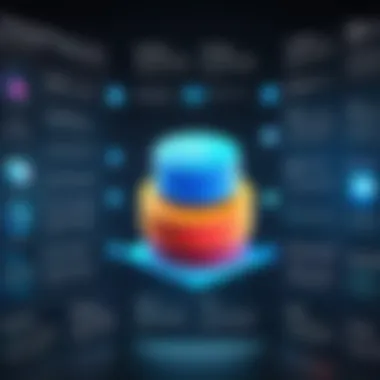
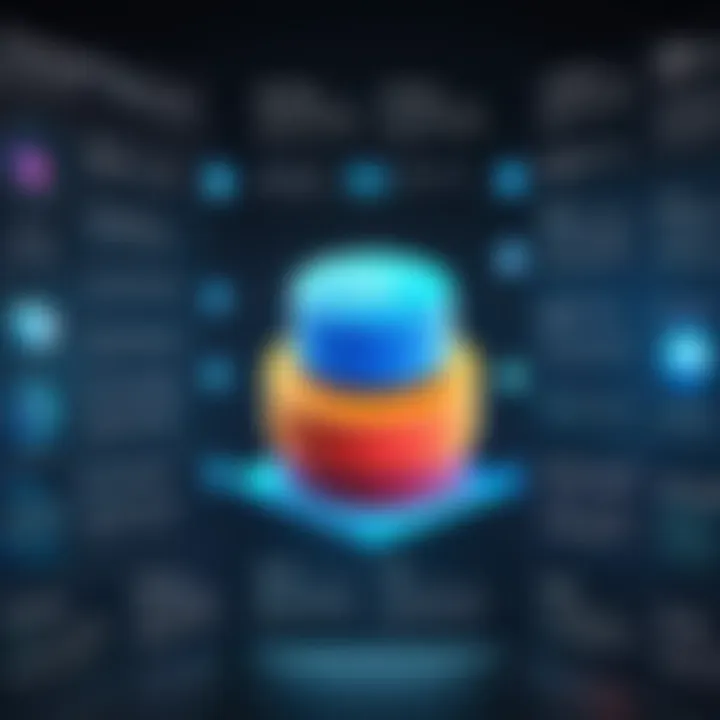
Case studies provide invaluable insights into the real-world applications of process simulation programs. These examples illustrate not only the potential benefits of these systems but also spotlight the challenges faced during their implementation. Emphasizing specific case studies enriches the discussion around process simulation by offering tangible illustrations of successful applications and the lessons learned. Understanding these instances can guide professionals in making informed decisions about their simulation needs.
Successful Implementations
Successful implementations of process simulation programs showcase their versatility across diverse sectors. For instance, a leading automotive manufacturer utilized Simul8 to optimize their assembly line processes. By creating a detailed simulation of their assembly line, the company was able to identify bottlenecks that were causing delays in production. This insight led to the reorganization of the workflow, resulting in a 30% increase in productivity. The accuracy of the simulation facilitated decision-making and encouraged employee buy-in, as the data presented backed the proposed changes.
Another significant case involves a healthcare provider that employed AnyLogic to streamline patient flow in their emergency department. By simulating various scenarios, they were able to reduce patient wait times significantly. The ability to model different resource allocations and patient arrival patterns allowed the staff to optimize their scheduling and improve overall service delivery. The success of this implementation highlighted the necessity of including end-user engagement in simulations to enhance practical application and acceptance within the organization.
Lessons Learned
Examining the lessons learned from different implementations reveals critical factors that contribute to the success or failure of process simulations. One key takeaway is the importance of data accuracy. In a project involving FlexSim for a logistics company, reliance on incomplete data led to flawed simulations. This ultimately resulted in ineffective decision-making and project delays. Thus, ensuring that data is both comprehensive and accurate is paramount.
Another lesson is the role of training. In a manufacturing case, workers who were not adequately trained on how to interpret simulation results struggled to utilize the information effectively. As a result, the organization faced resistance to changes that were proposed based on the simulation outputs. Training programs tailored to different levels of technical expertise can bridge this gap, empowering employees and reducing resistance.
"Practical testing combined with employee training ensures a robust implementation of simulation programs, fostering both innovation and acceptance within the workplace."
Lastly, the integration process itself is critical. In several scenarios, the lack of alignment between existing systems and the simulation software caused disruptions. Early involvement of IT departments can facilitate smoother integrations. Aligning the objectives of the simulation project with the broader organizational goals is also essential.
Future Trends in Process Simulation
Future trends in process simulation are becoming increasingly vital. As technology evolves, the necessity for effective and efficient simulation processes grows. Organizations need to adapt to these changes to maintain a competitive edge. This section explores the implications of advancements in process simulation.
Impact of Artificial Intelligence
Artificial Intelligence is reshaping how process simulations are designed and implemented. AI enhances model accuracy through advanced algorithms that analyze vast amounts of data. In practice, AI can help identify patterns and predict outcomes, promoting proactive decision-making.
Key benefits of integrating AI in process simulation include:
- Improved Predictive Capabilities: AI algorithms can predict results based on various scenarios, reducing the time required for trial-and-error methods.
- Automation of Routine Tasks: By automating repetitive modeling tasks, professionals can focus on complex analyses instead of mundane operations.
- Enhanced Optimization: AI-driven simulations continuously learn from past data, optimizing processes more effectively than traditional methods.
As AI evolves, its impact in the field of process simulation will only deepen, requiring professionals to update their skills and knowledge.
Advancements in User Interfaces
User interface design is a critical component of process simulation programs. A well-designed interface facilitates user engagement and enhances usability. Recent trends emphasize simplicity and intuitiveness in user interfaces. These advancements allow even non-experts to navigate complex simulations effectively.
Considerations for UI improvements include:
- Visualizations: Enhanced graphical representations help users understand intricate models at a glance. Tools that display simulation data visually can drastically improve comprehension.
- Interactive Elements: Incorporating interactive features lets users modify variables in real-time, providing immediate feedback on changes. This interactivity fosters a deeper understanding of the system being modeled.
- Accessibility: Ensuring that simulations run smoothly across various devices increases accessibility for team members, regardless of their technical backgrounds.
Integration with Other Technologies
Integrating process simulation with emerging technologies is paramount for future developments. This approach not only maximizes functionality but also enhances the overall performance of processes. Technologies such as IoT (Internet of Things) and cloud computing are examples of systems that can be integrated with simulation programs.
Benefits of integration include:
- Real-Time Data Utilization: IoT devices can provide real-time data to simulation models, allowing users to make informed, data-driven decisions.
- Scalability: Cloud computing enables organizations to scale their simulation capabilities without heavy investment in infrastructure. This scalability allows for flexible modeling solutions that adapt to changing business needs.
- Comprehensive Analysis: By combining simulation outputs with data analytics tools, businesses can analyze complex interactions between various systems.
The End
In any discussion surrounding process simulation programs, the conclusion serves as a pivotal element that consolidates previous insights. This section encapsulates the essence of the article and emphasizes the significance of understanding process simulations in today’s complex and dynamic environments.
A comprehensive grasp of these tools enables stakeholders not only to optimize workflows but also to enhance operational efficiency across diverse industries. This ability to simulate processes gives businesses a competitive edge, allowing for better decision-making based on predictive analytics and robust modeling methodologies.
Moreover, the adaptability of simulation programs means that they can be tailored to satisfy the unique demands of different sectors, whether it is manufacturing, healthcare, logistics, or energy. This versatility highlights the relevance of simulation in addressing industry-specific challenges and making informed strategic choices.
"An understanding of process simulations is not merely an accessory; it is vital for informed decision-making in an increasingly data-driven world."
Summarizing Key Takeaways
- Process Simulation Programs Are Essential: These tools are critical for continuous improvement in operations, offering detailed modeling capabilities.
- Diverse Applications: The versatility of these programs allows for applications across multiple industries. Each industry can leverage unique benefits from process simulation.
- Advantages and Limitations: While simulation programs offer cost reduction and enhanced insight, users must also navigate challenges regarding implementation and validation.
- Future Trends: Innovations such as artificial intelligence and improved user interfaces are set to revolutionize how these simulations are utilized.
- Implementation is Key: A well-planned approach to implementing simulation programs will maximize their potential benefits.
Final Thoughts on Implementation
Implementation of process simulation programs is more than selecting software; it is about aligning these tools with specific business goals. Organizations must start with a clear understanding of their objectives and the problems they aim to solve. The right software choice then becomes a matter of compatibility with existing systems and processes.
Training is also paramount. Ensuring that relevant personnel are well-versed in simulation methodologies will foster a culture of informed decision-making. This leads to better outcomes and allows organizations to make full use of simulation capabilities.
Additionally, ongoing evaluation of the simulation results will ensure that they remain relevant and actionable. This creates a feedback loop that continuously informs improvements and adaptations in operations.
In summary, effective implementation involves meticulous planning, appropriate tool selection, and continuous learning to ensure that process simulations serve their intended purpose.
Citing Relevant Literature
Citing literature relevant to process simulation ensures that the claims made throughout the article are substantiated by authoritative sources. This practice enriches the discourse by incorporating diverse perspectives and established research findings. When referencing industry studies, academic papers, or case analyses, it can provide the context needed to appreciate the nuances of process simulation.
Benefits of appropriate citations include:
- Credibility: Establishing trust with the audience by supporting points with recognized sources.
- Research Facilitation: Offering readers pathways to further inquiry and exploration of the methodologies discussed.
- Contextual Understanding: Providing a background that informs the application of various simulation techniques in different settings.
An example of a key reference could be articles from peer-reviewed journals on simulation methodologies. Such literature often showcases cutting-edge research and advancements in simulation techniques, which can inspire practitioners looking to adopt or enhance their strategies.
Further Reading Recommendations
For those interested in understanding more about process simulation, several resources can enhance your grasp of this powerful tool. Recommended further reading may include:
- Books on Systems Engineering: These offer insights into comprehensive methodologies that span across various industries and processes.
- Technical Papers on Algorithm Design: Exploring algorithm innovations can provide knowledge about the latest trends in simulation performance and accuracy.
- Industry Reports: Publications from organizations like Gartner or McKinsey often discuss contemporary use cases and best practices in process simulation.
- Online Platforms: Websites like Wikipedia and educational sites are great starting points for obtaining definitions and general knowledge about simulation tools. Reddit can offer community experiences and real-world applications that are beneficial for practitioners.
In summary, a well-curated reference section serves multiple purposes, aiding in the validation, exploration, and understanding of process simulation programs. For readers seeking to implement these tools effectively, the right literature can be pivotal in shaping their strategies and decisions.