Understanding Warehouse Management Systems in Shipping
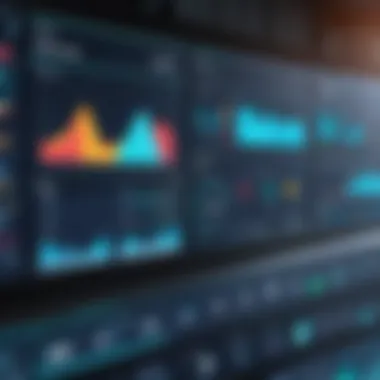
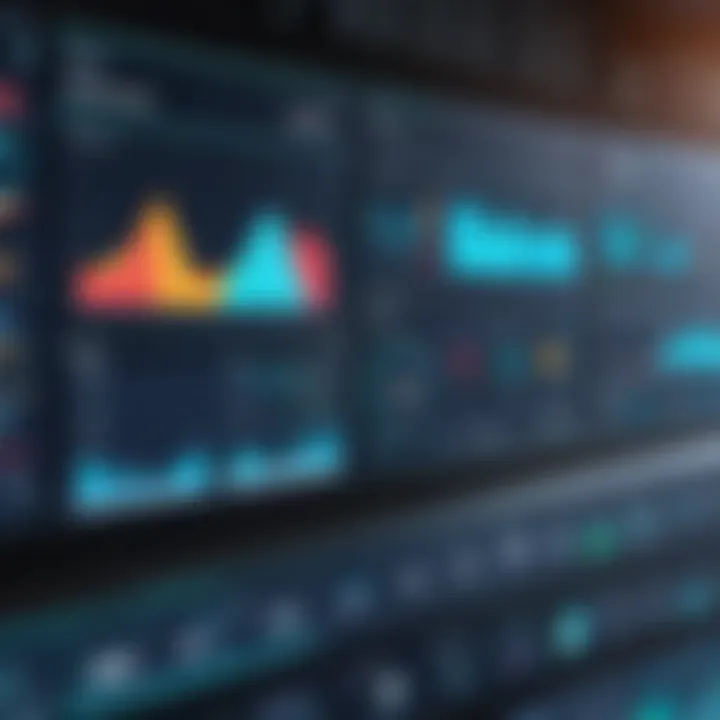
Intro
In an age where efficiency is king and the climax of operational success lies in swift shipping and precise inventory management, Warehouse Management Systems (WMS) have stepped into the limelight. These systems form the backbone of modern logistics, underpinning activities that resonate across industries. By leveraging advanced software solutions, businesses can navigate the intricate maze of warehousing, from inventory accuracy to seamless order fulfillment, with relative ease.
Understanding WMS shipping is not just about familiarizing oneself with software functions but also involves grasping the fundamental changes in logistics paradigms. As consumer demands morph and digital transformations become standard, the unique challenges that arise must be adequately addressed. Moreover, small to medium-sized enterprises (SMEs) are eager for practical, tailored solutions that can boost operational performance. Therefore, this article seeks to unravel key facets of WMS in shipping, contextualizing its significance within the broader landscape of supply chain management.
Overview of Key Features
Essential Software Capabilities
When delving into the realm of WMS, it's pivotal to spotlight the essential capabilities that set these systems apart from traditional inventory management. A robust WMS typically includes features like:
- Real-time tracking: This allows businesses to monitor shipments and stock levels as they happen, eliminating surprises and enhancing responsiveness.
- Automated inventory replenishment: With algorithms set to analyze demand patterns, the system can predict stock needs and reorder in a timely manner.
- Order management: This helps streamline the picking, packing, and shipping processes, ensuring that orders are fulfilled accurately and quickly.
- Reporting and analytics: Beyond mere number-crunching, many WMS solutions offer insights that can drive strategic decision-making, identifying bottlenecks and inefficiencies.
These core capabilities not only facilitate operational efficiency but also nurture flexibility in response to market changes and consumer requests.
Unique Features that Differentiate Options
Not all Warehouse Management Systems are created equal, as various platforms introduce unique features tailored to specific industry needs. For instance, some systems may incorporate integrated shipping modules that allow businesses to automate carrier selection and label generation, optimizing cost and time. Others might offer flexible integration capabilities with existing ERP systems, providing a cohesive digital infrastructure that supports uninterrupted work.
In sum, understanding these different aspects can help organizations make informed choices when selecting a WMS that fits their operational goals.
User Experience
Interface and Usability
An often overlooked but crucial aspect of WMS is user experience. A well-designed interface can drastically reduce the learning curve for staff. Systems that employ a clean layout and intuitive navigation empower users to perform tasks efficiently without extensive training. Features like drag-and-drop functionalities for inventory allocation or guided workflows greatly improve the usability of these complex systems.
Support and Community Resources
Adopting a new WMS is akin to bringing home a new pet; it requires care, guidance, and—most importantly—support. Many top-tier solutions come with dedicated customer service that can help with troubleshooting and project implementation. Furthermore, community forums and resources such as reddit.com or Facebook groups offer additional support from fellow users. Engaging with this community enables users to share insights, experiences, and tips that can alleviate common challenges encountered in WMS management.
Prelims to WMS Shipping
In the intricate world of logistics and supply chain management, Warehouse Management Systems (WMS) have emerged as a cornerstone for transforming how businesses handle their shipping processes. The significance of WMS in shipping cannot be overstated; it encompasses everything from inventory management to order fulfillment, gaining momentum as organizations seek to streamline their operations.
Definition of WMS
Warehouse Management Systems are software applications designed to manage and control warehouse operations. They assist businesses in optimizing inventory levels, improving order accuracy, and increasing the overall efficiency of their logistics processes. By centralizing operations, WMS provides real-time visibility into stock levels and locations, allowing companies to make informed decisions based on accurate data. This clarity is paramount, particularly in environments where timing is everything, and a single oversight could lead to delays or lost sales.
Understanding WMS starts with appreciating its multifaceted capabilities. It’s not just about keeping tabs on what’s in a warehouse; it encompasses sophisticated methods to ensure that the right products are in the right place at the right time.
Importance of Shipping in Supply Chain Management
Shipping serves as the final link in the supply chain chain and plays a crucial role in determining customer satisfaction and operational efficiency. The essence of shipping in the supply chain is underscored by its impact on:
- Cost Efficiency: Reducing shipping costs can massively affect a company's bottom line. Effective WMS software can help companies identify the best shipping rates and routes, cutting expenses.
- Speed of Fulfillment: In a world where customers expect rapid delivery, WMS can automate shipping processes, ensuring orders are fulfilled quicker and more accurately.
- Inventory Management: Ensuring that products are available for shipping when needed is vital. WMS helps prevent stockouts and overstock situations, creating a harmonious balance.
In a nutshell, introducing WMS in shipping not only aids businesses in maintaining competitive advantages but also enhances overall operational agility.
"The right WMS can be the difference between a chaotic warehouse and a well-oiled shipping machine."
The growing adoption of WMS by businesses of all sizes illustrates the vital role it plays in modern shipping strategies. As the landscape evolves, understanding its components becomes essential for optimizing supply chains, driving growth, and fostering customer loyalty.
Components of WMS in Shipping
Understanding the building blocks behind Warehouse Management Systems (WMS) is crucial for grasping their role in shipping logistics. The components of WMS not only streamline operations but also serve as the backbone for efficient shipping processes. With a keen focus on the intricacies of inventory management, order processing, and shipping modules, businesses can reap significant advantages in their supply chain management. Each component has its own set of functionalities that contribute to an overarching system aimed at reducing errors and improving responsiveness.
Inventory Management
Inventory management lies at the heart of a well-functioning WMS. It is the practice of overseeing stock levels, orders, sales, and deliveries in real time. When a system efficiently tracks inventory, it directly influences the capacity to fulfill customer demands. A few key aspects include:
- Real-time visibility: A robust WMS provides accurate and immediate insights into stock levels. Knowing what’s on hand helps prevent stockouts and overstock scenarios, which can both hurt a business's bottom line.
- Automated updates: With inventory changes being recorded automatically as transactions occur, businesses avoid the headaches that come with manual entry errors. This automation not only saves time but enhances accuracy.
- Adaptive storage strategies: WMS helps in dynamically optimizing storage allocations based on usage patterns. This approach ensures that high-turnover items are easily accessible, minimizing picking time and improving efficiency.
Efficient inventory management cultivates a predictable flow of goods, which is indispensable in today’s fast-paced market.
Order Processing
Order processing comprises the steps necessary to fulfill a customer’s order. A well-structured WMS enhances the process from order receipt to delivery. The benefits of effective order processing within WMS include:
- Streamlined workflows: A systematic approach minimizes the risk of miscommunication between departments. By automating workflows, companies can ensure that everyone is on the same page, reducing delays and errors.
- Batch processing: Instead of processing orders one at a time, systems can handle batches, greatly speeding up fulfillment. This feature suits businesses with high order volumes, allowing them to keep up with customer demand without compromising quality.
- Configurable rules: WMS often allows setups for priority handling based on factors like shipping destinations or customer preferences. Configurable rules help maximize resources, ensuring order fulfillment aligns with business objectives.
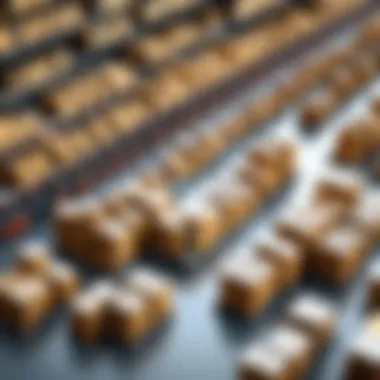
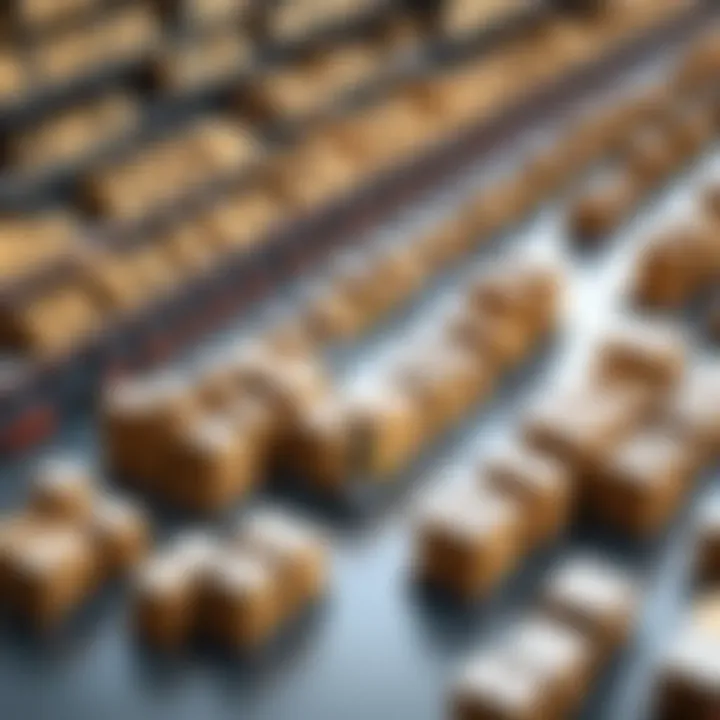
The smooth operation of order processing impacts not only internal efficiency but also customer satisfaction on a larger scale.
Shipping Modules
Shipping modules serve as the final link between warehouse processes and customer deliveries. They encompass various functionalities designed to ensure that freight reaches destinations swiftly and accurately. This piece of the WMS features:
- Carrier integrations: Direct integration with multiple carriers can streamline shipping decisions. Businesses can automatically select the most cost-effective and timely shipping options for different orders, enhancing overall delivery responsiveness.
- Labeling and documentation: Effective modules include automated label generation and documentation preparation, which constitute a significant part of shipping. Reducing manual tasks in this area helps prevent delays in the delivery chain.
- Shipping analytics: Advanced WMS shipping modules offer insight into shipping performance, allowing businesses to identify trends, calculate costs, and improve future shipping strategies.
In the realm of logistics, shipping modules are critical for maintaining the integrity of delivery promises.
"A well-integrated WMS bridges the gap between supply chain components and ensures that every process functions harmoniously."
These elements—inventory management, order processing, and shipping modules—intertwine to form a cohesive WMS. Opting to invest in these components transforms logistics into a finely tuned operation, poised to pivot and adapt as market demands shift.
Key Features of WMS Shipping
In today’s fast-paced logistics environment, the Key Features of Warehouse Management System (WMS) Shipping serve as the backbone for smooth operations. These features are not just fancy bells and whistles; they embody the essential tools needed for efficiency and accuracy in shipping processes. When businesses implement WMS, they gain leverage over several aspects, from real-time data tracking to comprehensive reporting capabilities. With e-commerce on the rise, having a system that actively supports shipping requirements is paramount. In this section, we’ll delve into the specifics of real-time tracking, automated reporting, and internet connection with other systems.
Real-Time Tracking
Real-time tracking is a game-changer in the logistics landscape. It involves the ability to monitor shipments as they move through the supply chain. Companies utilizing real-time tracking can pinpoint the location of goods at any moment. This feature enhances supply chain visibility and can lead to quicker decision-making.
This kind of transparency is invaluable. For example, consider a business managing hundreds of shipments on a daily basis. If a package goes missing along the route, real-time tracking enables immediate action—minimizing delays and keeping customers informed. Businesses survive on timely deliveries, and alerts sent directly to logistics managers can ensure proactive steps are taken.
"In an era where information is king, having immediate access to shipment status can differentiate between satisfied customers and those who feel left in the dark."
Automated Reporting
Another essential feature of a robust WMS is automated reporting. Imagine having to sift through piles of data to identify trends and performance metrics—tedious, right? Automated reporting takes this burden off shoulders. It generates reports on key performance indicators (KPIs), stocking levels, and order fulfillment rates in mere minutes.
For instance, a small business might schedule daily reports to gauge how many packages shipped on a given day. This reporting can also highlight patterns over time—such as peak shipping periods—which can inform staffing decisions and inventory management strategies. These reports can be tailored, ensuring that relevant stakeholders receive the insights they need without navigating through unnecessary data.
Integration with Other Systems
The efficacy of WMS shipping is significantly amplified when integrated with other business systems. By meshing seamlessly with Customer Relationship Management (CRM), Enterprise Resource Planning (ERP), or even Retail Management Systems, WMS ensures information flows freely. This avoids the frustrating silos that can lead to inaccuracies and miscommunication.
For companies, a well-integrated WMS allows for lightning-fast responses to changes in customer demand or inventory levels. Let's say an unexpected surge in orders occurs. If the WMS is linked with the ERP system, it can automatically adjust order processing and stock levels in real-time, keeping operations smooth.
In summary, the Key Features of WMS Shipping are fundamental to achieving operational excellence. As businesses navigate the complexities of supply chain management, these features stand out as essential to driving growth, reducing errors, and enhancing overall customer satisfaction. Efficient shipping nowadays is synonymous with having the right tools and practices in place.
Benefits of Implementing WMS in Shipping
Implementing a Warehouse Management System (WMS) in shipping is more than just a technical upgrade; it’s a strategic move that can lead to numerous advantages. For businesses navigating the choppy waters of logistics and supply chain management, understanding these benefits is crucial. Companies that invest in a WMS find themselves better positioned to respond to market demands while maintaining operational efficiency. Let's break down some of the most significant benefits.
Cost Reduction
One of the first benefits that leaps out is cost reduction. Shipping costs can quickly spiral out of control if not managed properly. A WMS provides tools to minimize these expenses through efficient inventory management. For instance, optimizing storage space within the warehouse often leads to reduced handling and transportation costs. Companies can keep track of products in real-time, ensuring that stock levels are maintained without overstocking. This practice drives down storage costs and reduces wastage due to expired or obsolete inventory.
Moreover, automation of processes helps negate human errors that can lead to costly mistakes, such as shipping the wrong product or miscalculating shipping fees. To see this in action, consider a mid-sized eCommerce business that integrated a WMS. They reported a dramatic decrease in shipping errors and associated costs within just a few months—an invaluable success story.
Improved Accuracy
Accuracy is non-negotiable in shipping and logistics. A WMS helps ensure that every item is accounted for, from the moment it enters the warehouse until it is shipped out to the customer. Using barcode scanning and RFID technology, a WMS facilitates precise tracking of each item. When discrepancies do occur, the system can quickly highlight them, allowing for immediate corrective actions.
Taking this a step further, accurate inventory levels lead to better order fulfillment rates. This means fewer backorders, which can frustrate customers and harm a business’s reputation. Imagine a scenario where a customer orders a product, and the store is able to promise delivery because the stock is tracked flawlessly. In a world where time is money, maintaining such accuracy can set a company apart from competitors.
Enhanced Customer Satisfaction
In today's marketplace, customer satisfaction stands as a cornerstone of success. The speed and accuracy with which orders are fulfilled directly impact customer experience. When a WMS is in place, businesses can guarantee that orders are shipped efficiently and accurately, resulting in timely deliveries. Happy customers are likely to return and recommend services to others, enhancing brand image and driving growth.
Additionally, WMS permits better communication with customers regarding their order status. Automated notifications can keep them in the loop—from dispatch to delivery. This transparency fosters trust and builds long-term relationships. Picture a customer receiving real-time updates about their shipment. It’s an assurance that their package is in good hands.
"A satisfied customer is the best business strategy of all." - Michael LeBoeuf
Challenges in WMS Shipping Implementation
Implementing a Warehouse Management System (WMS) in shipping isn't just a simple plug-and-play affair. It brings with it a basket of challenges that need close consideration. Understanding these challenges is vital for organizations aiming to streamline shipping processes, ensure accuracy, and drive efficiency. Let's dig into three key hurdles that businesses often encounter: resistance to change, integration issues, and the cost of implementation.
Resistance to Change
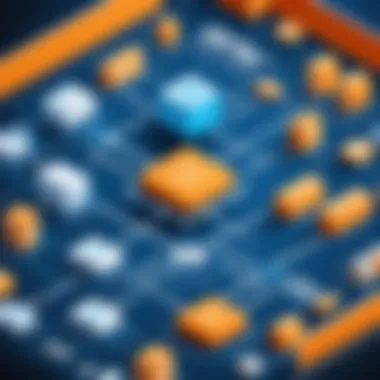
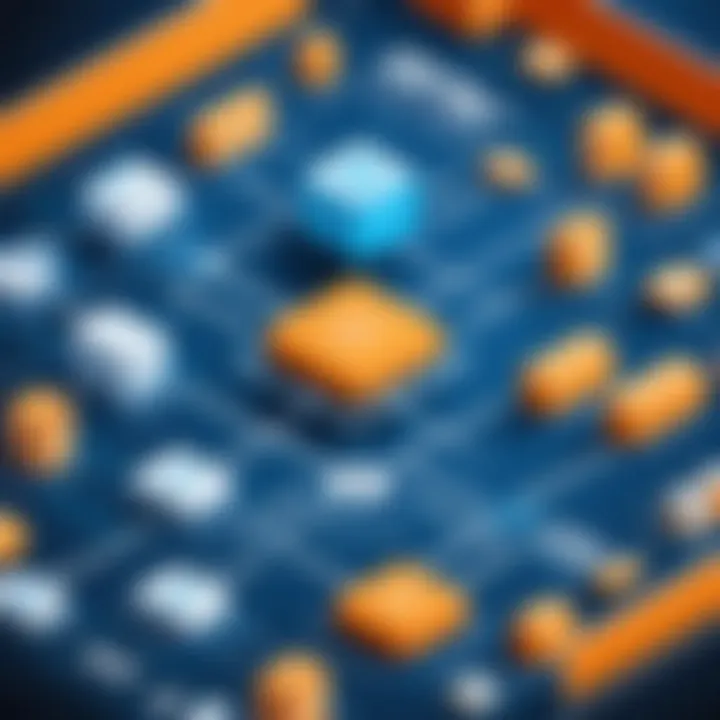
One of the most common obstacles in adopting WMS solutions is the human element—often referred to as resistance to change. Employees may feel a sense of uncertainty when confronted with the prospect of using new technologies.
Adopting a WMS requires staff to learn new systems and processes, which can lead to anxiety, especially among long-time employees accustomed to traditional methods. Often, this hesitation stems from a general dislike of disruption and the fear of inadequacy in mastering the new technology.
To cater to this apprehension, organizations should prioritize communication. Ensuring that employees understand the reasons behind the switch, such as improved efficiency or accuracy, goes a long way. Training programs are also essential. When staff feel equipped to handle new tools and processes, the transition tends to go smoother.
Integration Issues
The next hump in the road often involves integration issues. A WMS won't function in isolation; it needs to operate alongside other systems, such as enterprise resource planning (ERP) solutions or customer relationship management (CRM) platforms.
Integrating these disparate systems can be like fitting a square peg in a round hole. Compatibility issues may arise, impacting data flow and communication across platforms. Such snags can lead to data silos and create inconsistencies in inventory tracking or order processing.
To sidestep integration troubles, an assessment of existing systems should come first. It’s crucial to choose a WMS that supports API or EDI connectivity to facilitate seamless data exchange. More importantly, consulting integration specialists can provide the expertise needed to align all systems harmoniously.
Cost of Implementation
Implementing a WMS system isn’t also without its monetary challenges. The up-front investment can be quite daunting. This includes software purchase, hardware, and training costs. Then there's the maintenance and support fees which can accrue over time.
Many businesses may balk at these initial costs, viewing them as a financial strain. However, it’s important to look at the long-term return on investment (ROI). The right WMS can drastically cut down on operational costs through improved accuracy, efficiency, and reduced labor hours.
To ease the financial burden, organizations should consider phased implementations. Gradually introducing the system allows for better budgeting and fewer shocks to the bottom line.
"With proper planning and execution, the challenges posed during WMS shipping implementation can transform into stepping stones for achieving greater operational excellence."
In summary, tackling the challenges of WMS implementation requires a well-thought-out strategy that emphasizes communication, technical compatibility, and financial planning. When these elements are aligned, businesses not only improve their shipping operations but also position themselves for long-term success.
Future Trends in WMS and Shipping
The landscape of Warehouse Management Systems (WMS) in shipping continues to be dynamic, adapting to fast-paced changes in technology and consumer expectations. This section will explore critical trends that are reshaping how businesses manage logistics and shipping processes. By focusing on enhancements in technology, automation, and sustainability initiatives, we can comprehend how these elements will benefit organizations and cater to an ever-evolving marketplace.
Advancements in Artificial Intelligence
Artificial intelligence is rapidly transforming WMS shipping in ways that few could have predicted just a few years ago. The use of AI enables warehouses to improve decision-making processes by analyzing large datasets quickly and efficiently. This is not just a passing trend; it’s the backbone of smarter shipping.
For instance, predictive analytics can forecast demand more accurately, allowing businesses to align inventory with market needs. There's a real value in this, as it significantly reduces the risks of overstocking or stockouts. Moreover, AI-driven algorithms can optimize picking routes in the warehouse, leading to more productive use of time and resources.
Additionally, machine learning can learn from past shipping patterns, making real-time adjustments to logistics strategies. This is crucial; it could save a company from losses due to late shipments or misplaced orders.
Increased Use of Automation
Automation is no longer a luxury but a necessity in today’s WMS environment. Organizations are increasingly adopting robotic processes to streamline operations. Automated solutions reduce human error, improve efficiency, and cut down on operational costs.
You might find automated guided vehicles (AGVs) in modern warehouses, playing a vital role in the transportation of goods. These robots can move products from one area to another without human intervention. In addition, automated inventory systems ensure real-time tracking, bridging gaps between order placement and fulfillment.
While some might balk at the initial investment, the long-term cost savings and efficiency improvements are hard to argue against. Businesses can scale at a faster pace and respond to fluctuating market demands with a nimbleness that manual processes simply cannot match.
Sustainability Initiatives
In an era where climate concerns are at the forefront, sustainability initiatives are becoming essential in WMS shipping. Many companies are reevaluating their supply chains to reduce their carbon footprints. This includes everything from packaging to transportation methods.
Adopting more environmentally friendly packaging solutions, like biodegradable materials or minimalistic designs, not just appeals to eco-conscious consumers but also helps in complying with regulations. Moreover, using energy-efficient transportation methods can significantly reduce emissions, aligning with global sustainability goals.
Companies are also using data analytics to optimize shipping routes. By choosing the most efficient pathways for transportation, they reduce fuel consumption and operational costs. Ultimately, sustainability is no longer just about doing the right thing; it’s increasingly becoming a business imperative.
"Sustainable practices in shipping not only cater to the growing consumer base that prioritizes eco-friendliness but also foster innovation in logistics strategies."
In summary, the future of WMS shipping hinges on advancements in artificial intelligence, increased automation, and the pivot towards sustainability. These trends not only enhance operational efficiency but also position businesses as leaders in a highly competitive space.
Practical Steps for Implementing WMS
Implementing a Warehouse Management System (WMS) is not just a technical upgrade; it’s a crucial step toward optimizing operations and enhancing efficiency in shipping. You can't simply jump into the deep end without understanding the lay of the land first. The process requires deliberate, strategic steps to ensure that the system aligns with the unique demands of the business. Below are some specific elements and considerations that businesses need to take into account.
Assessing Business Needs
Before diving head-first into selecting a WMS, it’s imperative to pause and reflect on the specific needs of your business. Every company operates within its unique context, which influences its requirements from a WMS. By recognizing your operational goals, such as improving inventory accuracy or speeding up order processing, you can create a foundation for a tailored solution.
Ask yourself a few questions:
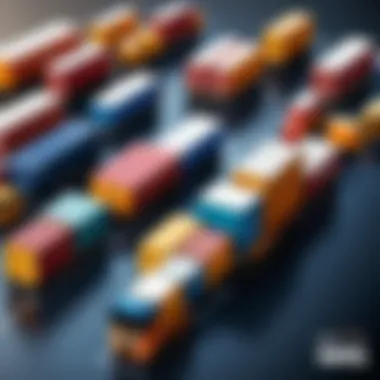

- What challenges currently hinder efficiency? Identifying bottlenecks in your current system can point you toward features and functions you absolutely need.
- What are your growth projections? Understand whether you will require a system that can scale as you expand.
- What are your budget constraints? Knowing how much you can invest will narrow your options significantly.
Engaging with various stakeholders in your organization—like warehouse staff, IT personnel, and management—helps paint a fuller picture of your needs. This collaborative approach avoids potential oversights and makes sure everyone is on board.
Selecting the Right Software
After assessing your specific business needs, it’s time to choose the software itself. This decision can feel like picking a partner for a long-term relationship; compatibility is key. Look for a WMS solution that offers flexibility and functionality tailored to your requirements.
When evaluating potential vendors, consider the following aspects:
- Scalability: Can the software grow with you? A solution that can't adapt will become a hindrance down the line.
- User-friendliness: Training costs and time can soar if the system is overly complex. Choose user-friendly interfaces for smoother onboarding.
- Integration capabilities: Ensure the WMS can work harmoniously with your existing technology stack, including ERP systems and supply chain management tools.
- Support and customer service: You want a vendor ready to assist when you hit snags, not one that leaves you high and dry.
Training Staff and Key Stakeholders
Once the software is selected, the next step involves properly equipping your team to use the new system effectively. Training is often an overlooked element of implementation but it is crucial for ensuring that the transition smooth. No one wants a situation where the shiny new system ends up collecting dust because employees are unsure how to fully utilize it.
A few points to think about include:
- Tailored training sessions: Offer training tailored to different user levels within the organization. Not everyone needs to know every screen in the software.
- Ongoing support: Have a procedure in place for ongoing learning, such as refresher courses or a dedicated help desk to address questions as they arise.
- Feedback loops: Create channels for employees to provide feedback on the training process and the system's performance. This will empower your team and help fine-tune the system further.
Ultimately, a well-trained workforce not only eases the adjustment period but also optimizes the functional potential of your new WMS.
*"A smooth sailing WMS implementation requires more than just software; it needs thoughtful planning, ongoing training, and a team willing to adapt."
By following these practical steps, businesses can lay the groundwork for a successful WMS implementation that enhances their shipping efficiency and operational capabilities.
Case Studies: WMS Shipping Success Stories
Understanding the practical impacts of Warehouse Management Systems (WMS) through case studies provides insightful perspectives on how businesses have transformed their shipping processes. These examples not only highlight the versatility of WMS in various settings but also demonstrate the tangible benefits that effective implementation can yield. Today's competitive environment demands innovation, and the success stories from small businesses and large enterprises show how adopting WMS solutions can lead to significant operational improvements.
Small Business Transformation
Consider a small organic grocery store, GreenLeaf Market, that struggled with inventory management and order fulfillment. Before implementing a WMS, the store relied on manual tracking. This approach led to constant stock-outs of popular items while others lingered unsold on shelves. Customers often left disappointed, which was bad for business. After deploying a tailored WMS solution designed for small enterprises, everything changed.
Real-time inventory tracking allowed GreenLeaf to maintain optimal stock levels, minimizing waste and maximizing sales. Automated order processing sped up the checkout experience, while accurate data reporting provided insights into customer preferences. The results?
- 30% Increase in Sales: Customers found their desired products in stock more often, driving repeat visits.
- Cost Savings: The store reduced spoilage costs significantly, reporting a nearly 25% drop in inventory losses.
- Customer Satisfaction: Feedback scores improved, with many customers applauding the availability of fresh produce.
GreenLeaf Market’s transformation illustrates how even a small-scale operation can achieve big results with WMS. In essence, it confirms that effective technology can empower smaller businesses to compete fiercely in saturated markets without breaking the bank.
Enterprise-Level Optimization
Now, let’s turn to a large corporation: LogisticsPal, a global freight company that handles millions of shipments annually. Prior to their WMS upgrade, the organization grappled with inefficiencies due to fragmented systems across various regions. Each department functioned independently, leading to mismatched information and slower response times.
After integrating a robust, centralized WMS across all operations, LogisticsPal experienced a remarkable transformation. Specifically:
- Enhanced Efficiency: Warehouse labor productivity improved by 40% due to streamlined processes.
- Inventory Accuracy: The accuracy of inventory audits went up to 99%, reducing overhead costs related to unsold items.
- Faster Shipping Times: With optimized pick paths and real-time tracking, shipping times fell by 20%, delighting customers.
"The upgrade to a comprehensive WMS not only consolidated our operations but also provided insights that were previously unattainable," noted Maria, an IT manager at LogisticsPal.
These case studies exemplify that whether you are a small business like GreenLeaf Market or a multinational company like LogisticsPal, WMS shipping solutions can significantly enhance operational efficiency and customer satisfaction. The key lies in choosing the right technology that aligns with one’s unique operational needs.
End
The conclusion serves as a critical component of the article, summarizing the significance and all encompassing insights surrounding Warehouse Management Systems (WMS) in shipping. Throughout the discourse, we've seen how WMS shines a light on operational efficiencies, offering a granular view into elements like inventory management and order fulfillment. The importance of understanding WMS cannot be overstated; as logistics become increasingly complex, having a solid grasp on these systems empowers businesses to optimize their shipping processes effectively.
Key insights from our analysis have illustrated that WMS provides numerous benefits, including enhanced accuracy in order processing and significant cost reductions. These features not only streamline operations but ultimately contribute to improved customer satisfaction – an essential factor in today's competitive landscape. After all, happy customers translate to repeat business and positive word-of-mouth, which can be invaluable for growth.
Additionally, the challenges of implementing WMS solutions—such as resistance to change and integration issues—were discussed. Recognizing these hurdles is pivotal for businesses, as proactive strategies can be established to mitigate potential setbacks. Organizations aiming to adopt or upgrade their WMS should approach these complexities with a strategic mindset, keeping their long-term goals in sight.
"Knowledge is power. Information is liberating. Education is the premise of progress, in every society, in every family." - Kofi Annan
In essence, bringing all these threads together reveals that WMS in shipping embodies a convergence of technology and best practices that facilitates a smoother operation in the supply chain. Companies that take the time to understand, integrate, and properly leverage these systems position themselves for profitability and adaptability in the ever-evolving marketplace.
Summarizing Key Insights
The journey through this exploration of WMS shipping hinges on several key takeaways:
- WMS enhances inventory control: Efficient management of stock levels is key to maintaining operations without hiccups. Accurate tracking helps in preventing excess inventory or stock-outs.
- Order fulfillment accuracy is paramount: Customers expect their orders to be processed without errors; WMS aids in achieving this through improved order tracking and picking accuracy.
- Integration with broader systems offers synergy: WMS doesn't operate in a vacuum. Its ability to integrate with other business systems—like ERP or TMS—creates a comprehensive framework for data management and operation efficiency.
- Cost savings contribute to fiscal health: By automating inventory and shipping processes, businesses often see reductions in labor costs and operational inefficiencies.
- Customer satisfaction drives repeat business: Ensuring that customers receive their orders promptly and accurately isn't just good service; it's a business strategy. Happy customers lead to loyal customers.
Recommendations for Future Considerations
Looking ahead, several recommendations stand out for organizations considering a WMS solution:
- Emphasize training and education: Ensure that staff are well-informed about the WMS features and capabilities. Their familiarity with the system will be crucial for maximizing its use.
- Assess the specific needs of the business: Not all WMS solutions are built the same. Conducting a thorough needs assessment can guide decision-making in selecting the right software.
- Stay agile in system upgrades: As technology evolves, so does the need for updates. Keeping the system current will ensure continued effectiveness and alignment with business goals.
- Monitor industry trends: Being aware of changes in technology, regulations, and customer expectations will help businesses adapt their WMS strategies proactively.
- Engage stakeholders: Maintain open lines of communication with all parties involved in the shipping process, from warehouse staff to higher management. Aligning everyone's goals ensures smoother cooperation and success.