Mastering Inventory and Warehouse Management
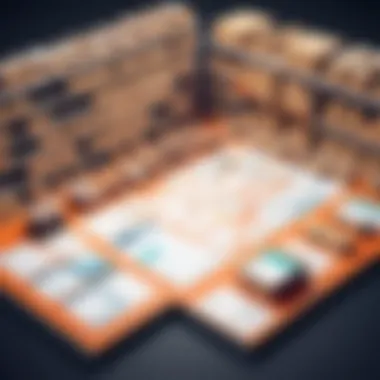
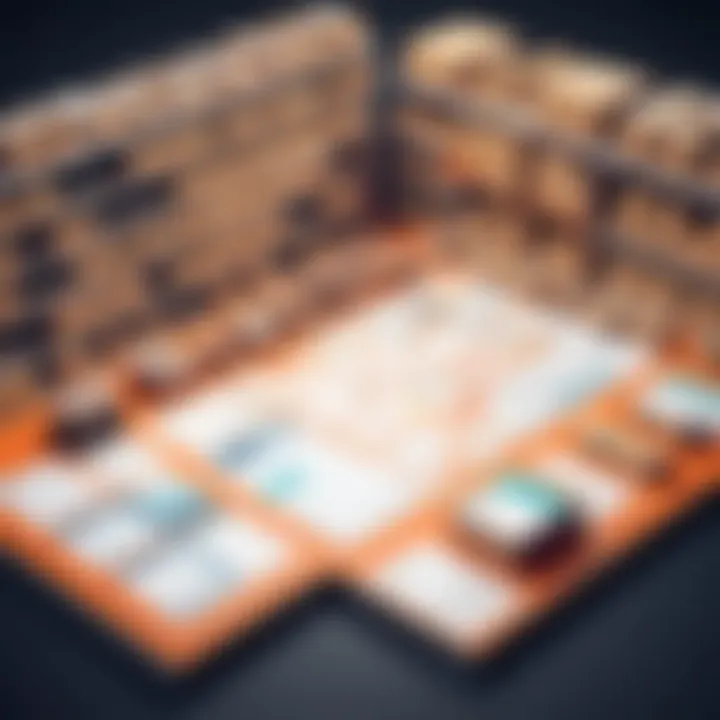
Intro
The landscape of modern business is increasingly shaped by efficient inventory and warehouse management practices. In an age where supply chains are more intricate, optimizing these aspects becomes critical for sustaining competitive advantage. Navigating through this complex terrain is essential for small to medium-sized business owners and technology managers who are looking to enhance their operations and make informed decisions regarding software solutions.
The delicate interrelationship between inventory management and warehouse management cannot be overstated. While inventory management focuses on tracking and controlling stock levels, warehouse management zeroes in on the logistics and physical storage of these products. Understanding the nuances of both is akin to knowing the ropes in a well-oiled machine where every cog has its specific role and responsibility.
In this article, we will demystify the critical features integral to inventory and warehouse management, explore the user experience associated with essential software, and underscore the strategies that businesses can implement to streamline their operations. This detailed investigation aims to equip our tech-savvy readership with actionable insights to cut through the noise and foster valuable improvements in their supply chain processes.
Defining Inventory Management
Inventory management is the backbone of any productive business, managing stock with the precision of a well-tuned engine. Understanding this concept means diving deep into its intricacies, recognizing how it intertwines with warehouse management. Effective inventory management is not merely about keeping track of stock; it's about ensuring that the right products are available at the right time, maximizing customer satisfaction while minimizing costs. The essence lies in striking a balance—a delicate act that requires astute insight and foresight.
Core Principles of Inventory Management
At the heart of inventory management are a few core principles that guide businesses toward achieving their goals:
- Accuracy: Keeping precise records is paramount. Inaccurate data can lead to overstocking or stockouts, both of which can strain finances.
- Optimization: Having too much inventory ties up cash and increases holding costs. On the flip side, too little can hamper sales. Finding that sweet spot means regularly analyzing demand trends and adjusting orders accordingly.
- Visibility: Access to real-time inventory data is essential. Businesses rely on tools and systems that provide insights into stock levels, allowing for proactive decision-making.
- Flexibility: The market constantly changes; hence, flexibility in inventory strategies facilitates quick adaptation to shifts in demand or supply chain disruptions.
These principles provide a foundation from which businesses can innovate and enhance their inventory strategies, ensuring they remain competitive in an ever-evolving landscape.
Inventory Types and Classifications
Inventory can be classified into various types, each serving a specific purpose within a business context. Understanding these categories is crucial for effective management:
- Raw Materials: These are the basic materials that are yet to undergo processing. Companies in manufacturing rely heavily on this type for production.
- Work-in-Progress (WIP): This category comprises items that are in the process of being manufactured. Tracking WIP is vital to understanding production flow.
- Finished Goods: The end products ready for sale belong in this category. Businesses often need effective strategies to manage these to meet customer demand promptly.
- Maintenance, Repair, and Operations (MRO): Supplies used in production operations but not a part of the finished product fall under this classification. Tracking MRO inventory ensures operational efficiency.
Each type serves a unique function and requires tailored approaches for management, ultimately affecting profitability.
The Role of Inventory in Business Success
Inventory plays a critical role in the larger tapestry of business success. While it may seem like a logistical hurdle at times, it’s also a vital asset. Here’s why:
- Customer Satisfaction: Having products readily available leads to improved customer experiences. Quick fulfillment leads to repeat business and brand loyalty.
- Cash Flow Management: Well-managed inventory provides insight into cash flows. Knowledge about stock levels and turnover rates helps businesses assess their financial health accurately.
- Strategic Planning: Understanding inventory trends allows for informed decisions about future growth and expansions. Businesses can plan promotional events around inventory types that are readily available.
Ultimately, managing inventory effectively transcends mere stock-taking; it nurtures the sustainable development of an enterprise, making it a critical factor in long-term success.
Exploring Warehouse Management
Warehouse management is a cornerstone of the broader field of supply chain management. It involves not just the storage of goods but also the principles that guide the efficient operations of this process. Understanding warehouse management is essential for businesses aiming to improve their logistics, reduce costs, and enhance customer satisfaction. In today’s market, a well-organized warehouse can be a real game changer. With nimble operations, businesses can quickly respond to customers’ needs and shifts in demand, making its exploration not just beneficial but crucial.
Fundamentals of Warehouse Management
At its core, warehouse management governs the operations and processes that keep goods flowing in and out of a facility. This includes receiving, storage, inventory control, order fulfillment, and shipping. Each function must operate in harmony with the others to ensure seamless transitions and maintain accuracy.
One key element is inventory tracking, which relies on various technologies such as barcode scanners or RFID systems. These technologies not only speed up the tracking process but also reduce human error. Knowing where everything is located at all times enables staff to act promptly and efficiently, unlocking the full potential of the warehouse.
Another important aspect is the management of warehouse staff. Well-trained personnel who understand the tools at their disposal can greatly enhance overall operational efficiency. Just like a well-oiled machine, every part must work together, from leadership right down to the last warehouse hand.
Key Functions of a Warehouse
Regardless of the kind of goods handled, certain functions are consistent across all warehouses.
- Receiving Goods: This function involves checking incoming shipments for accuracy and quality. It is crucial that this step is executed correctly to prevent future issues in the supply chain.
- Storage: Here, products are stored in designated areas, optimizing space based on size, weight, and turnover rates. Different goods may require different handling and storage conditions, such as temperature control for perishables.
- Inventory Control: Regular stock counts and audits are essential. Keeping an accurate count of items not only prevents stock discrepancies but also enables better forecasting and decision-making.
- Order Processing: This covers everything from picking the right items to packing and shipping. A cluttered, inefficient order processing workflow can lead to delays and customer dissatisfaction.
- Shipping: The final stage involves preparing goods for transport. This ensures that orders reach customers promptly, which can be a decisive factor in customer satisfaction.
The success of a warehouse hinges on how well these functions are executed.
Warehouse Layout and Design Considerations
The layout of a warehouse plays a significant role in operational efficiency. A thoughtfully designed layout can significantly enhance workflow, minimize bottlenecks, and improve safety.
When planning a warehouse layout, several factors come into play. These include:
- Flow of Goods: The movement of products should always be intentional. Layouts should facilitate a smooth flow from receiving to storage to shipping.
- Accessibility: Items frequently picked should be easily accessible. Products should not be hidden away in remote corners, creating additional work.
- Safety Regulations: Following safety guidelines not only protects your workforce but also minimizes liability issues. Utilizing adequate spacing between aisles helps to prevent accidents and allows safe passage for equipment.
- Scalability: As businesses grow, their warehouses must also adapt. Flexible design will allow for easy integration of additional shelving or storage options in the future.
- Use of Technology: Automated systems and layout designs should cater to the inclusion of technology to enhance operations further.
A well-planned warehouse layout fosters better performance, reduces waste, and can even save money in the long run. It is not just about where things go; it’s about deliberately maximizing every square foot for efficiency.
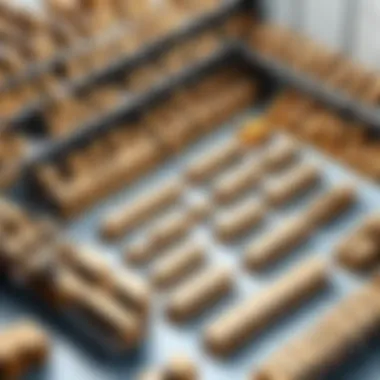
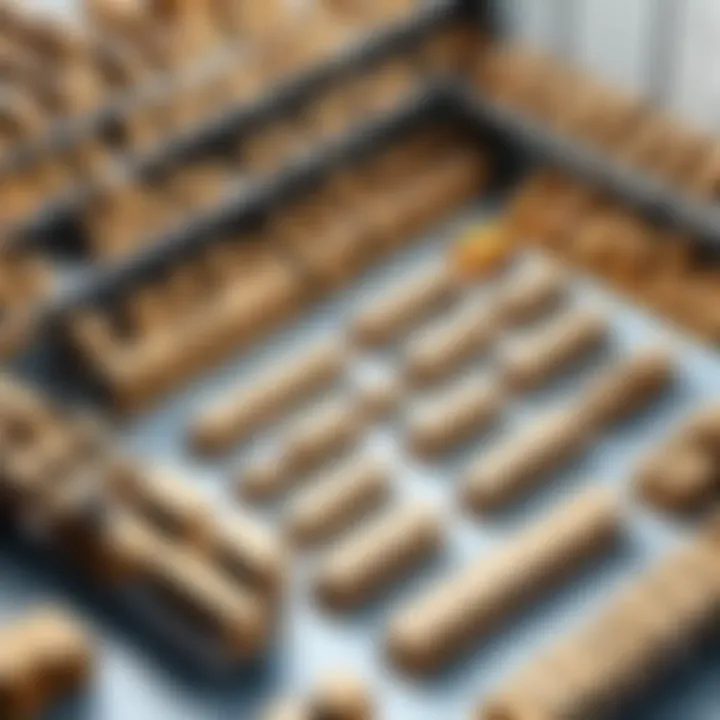
“An organized warehouse is not merely about storage; it's about creating a streamlined operation that serves as the backbone of customer fulfillment.”
In summary, the exploration of warehouse management offers substantial insights into optimizing operations and responsiveness in an increasingly competitive market. By understanding the fundamentals, key functions, and layout considerations, businesses can refine their strategies and improve overall performance.
The Relationship Between Inventory and Warehouse Management
In the realm of operational efficiency, the relationship between inventory and warehouse management stands as a cornerstone that can make or break a business. These two components do not exist in a vacuum; rather, they intertwine in a complex web of processes that ultimately influence a company’s bottom line. When inventory levels are meticulously matched with warehouse capacities, businesses can streamline their supply chain, reduce costs, and boost customer satisfaction. This holistic approach recognizes that inventory and storage are two sides of the same coin.
Key Elements in the Relationship
- Synchronization: Effective communication between inventory management and warehouse systems ensures that stock levels reflect actual availability. When the left hand knows what the right hand is doing, discrepancies are minimized.
- Real-Time Data Access: Modern businesses depend heavily on data analytics to manage stock levels. Timely information allows companies to adjust their inventory strategies based on current trends, thus enhancing responsiveness.
- Dynamic Adaptability: In the ever-changing landscape of business, adaptability is vital. The fluid exchange between inventory and warehouse management supports businesses in responding to market fluctuations, ultimately leading to improved operational resilience.
Interdependence of Inventory and Warehouse Systems
The interdependence between inventory and warehouse systems is nothing short of reciprocal. On one hand, inventory provides the necessary data that informs warehouse processes. On the other, warehouse operations impact how inventory is managed and stored.
One practical example is the use of Just-In-Time (JIT) inventory management. When a warehouse operates on the JIT model, it receives goods only as they are needed in the production process. This reduces costs associated with excess material handling and frees up valuable shelf space for essential items. However, this model hinges profoundly on the performance of both inventory and warehousing systems. Any hiccup in warehouse operations directly affects inventory availability and production timelines, potentially leading to significant delays.
Moreover, the relationship can be enhanced by embracing technology. Warehouse management systems (WMS) now integrate seamlessly with inventory management software.
Such integrations help in real-time tracking of stock levels, automatic reorder points, and precise forecasting of demand. By ensuring that warehouses are stocked appropriately, businesses can limit stockouts and avoid the pitfalls of overstocking.
Impact on Supply Chain Efficiency
The interplay between robust inventory management and warehouse operations yields a profound impact on supply chain efficiency. When these elements align effectively, the repercussions resonate throughout every aspect of the supply chain from production to delivery.
- Cost Control: A well-organized inventory reduces holding costs, minimizing waste and losses associated with obsolescence.
- Faster Turnaround Times: Optimal warehouse layouts enable quicker picking and packing, delivering goods to customers without unnecessary delays.
- Enhanced Customer Trust: Accurate stock levels and timely fulfillment contribute to a reliable service, nurturing customer confidence and loyalty.
"Efficiency isn’t about doing less; it’s about doing more of the right things."
This quote captures the essence of the relationship between inventory and warehouse management. By harmonizing these processes, businesses not only enhance their operational efficiency but also position themselves favorably in a competitive environment.
Ultimately, understanding and nurturing the relationship between inventory and warehouse management is pivotal for any business seeking to thrive in a fast-paced market. A well-oiled machine doesn't just work better; it sets the foundation for sustainable growth and customer satisfaction.
Challenges in Inventory Management
In today’s fast-paced business world, the effectiveness of inventory management can make or break a company’s bottom line. The challenges presented in effective inventory management often correlate directly with the operational efficiency and customer satisfaction levels. Understanding these challenges not only sheds light on underlying operational hurdles but also prepares businesses to confront them head-on. The implications of not addressing these challenges can range from increased carrying costs to diminished customer trust and loyalty.
Common Inventory Issues
A variety of challenges arise in the realm of inventory management. Some of the most frequently encountered issues include:
- Inaccurate Inventory Records: One common issue is having discrepancies between the actual physical inventory and the data recorded in the system. This can lead to misplaced products, delays in order fulfillment, and ultimately, dissatisfied customers.
- Slow-Moving Inventory: Understanding what inventory moves means keeping tab on stock that does not sell quickly. This can clog up storage space, leading to increased warehousing costs.
- Expired or Obsolete Inventory: Particularly in industries like food and pharmaceuticals, products can expire or become obsolete. Neglecting this can not only result in losses on stock but also negatively affect safety and compliance.
- Excess Stock: Holding onto more products than necessary can incur significant storage expenses and hurt cash flow. Over-ordering is often a big problem for businesses that fail to anticipate demand accurately.
These common issues signal the need for a refined approach to inventory management. Proper strategies implemented effectively can not only mitigate these problems but transform them into opportunities for growth.
Dealing with Demand Fluctuations
Demand fluctuations are yet another challenge that tests the resilience of inventory management systems. Changes in consumer preferences, seasonal trends, and economic shifts can lead to unpredictable spikes or drops in demand.
To navigate these fluctuations:
- Accurate Demand Forecasting: Employing analytics tools and software can greatly enhance the accuracy of demand forecasting. Proper data analysis allows businesses to anticipate changes and adapt their inventory policies accordingly.
- Agile Inventory Practices: The implementation of an adaptable inventory system can help businesses pivot quickly in response to sudden changes. This approach requires flexibility in both inventory procurement and distribution channels.
- Safety Stock: Maintaining a buffer stock can help guard against unexpected rises in demand. However, it is crucial to calculate this carefully to avoid excessive holding costs.
By acknowledging and preparing for demand fluctuations, businesses can better position themselves to meet their customer’s needs without compromising their financial sustainability.
Mitigating Stockouts and Overstocks
Finding the right balance between stockouts and overstocks is a delicate dance that affects inventory efficiency. Stockouts, which occur when inventory levels fall to zero, can lead to missed sales and a damaged reputation. On the other hand, overstocks can drain cash flow and increase storage costs. Here’s how to mitigate both:
- Real-Time Inventory Monitoring: Utilizing inventory management software that provides real-time updates can aid businesses in keeping track of stock levels, identifying trends, and making timely purchasing decisions.
- Just in Time (JIT) Inventory: This system emphasizes ordering stock only when it is needed for production, thus minimizing the risk of overstock while ensuring that the inventory is available when required.
- Supplier Relationships: Developing strong relationships with suppliers can provide more flexibility and quicker replenishment options, which is helpful when dealing with sudden spikes in demand.
"An efficient inventory management system is not just about having the right products on hand; it’s about understanding and responding to the market dynamically."
Navigating the challenges of inventory management involves a multi-faceted approach rooted in strategy, flexibility, and proactive measures. By confronting common inventory issues, adjusting to demand fluctuations, and maintaining an equilibrium between stockouts and overstocks, businesses can elevate their operational success.
Modern Technologies in Inventory and Warehouse Management
In today’s fast-paced marketplace, staying ahead of the curve is paramount for businesses involved in inventory and warehouse management. With evolving consumer expectations and global competition, leveraging modern technologies is no longer just a luxury but a necessity. These technologies not only streamline operations but also enhance accuracy and efficiency. When done right, incorporating technological solutions can significantly cut costs and improve customer satisfaction in the long haul.
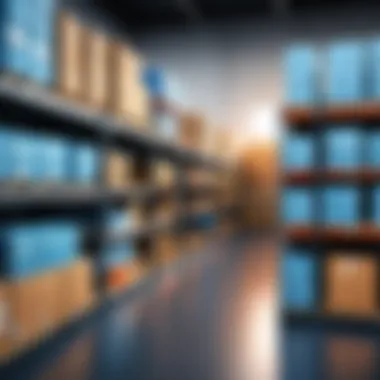
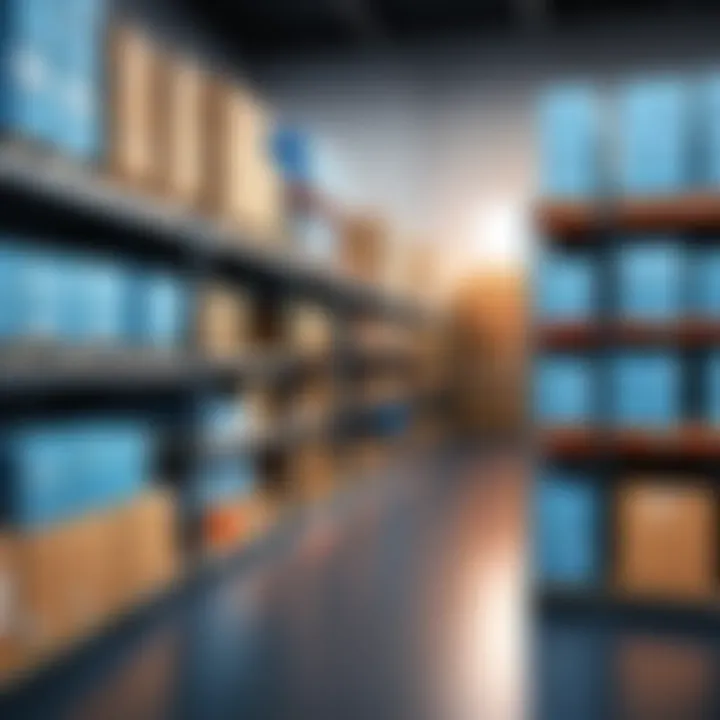
The integration of modern technologies in inventory and warehouse management encompasses several key elements:
- Software Solutions: Advanced inventory management systems centralize data and offer real-time visibility into inventory levels, making it easier to manage stock effectively.
- Automation: Robotics and automated guided vehicles (AGVs) can handle repetitive tasks, reducing human error and enabling quicker processing of orders.
- Data Analytics: Gathering and analyzing data can reveal patterns and trends that inform better decision making across the supply chain.
Beginner’s Guide to Inventory Management Software
Navigating inventory management can feel like a maze, especially for newcomers. The right software can illuminate the path forward. Inventory management software helps streamline processes by automating tasks such as tracking stock levels, managing orders, and generating reporting. When selecting software, consider factors like scalability, user-friendliness, and integration capabilities with other systems.
Some popular options to consider are:
- TradeGecko: Known for its easy-to-use interface and ability to scale with your business.
- NetSuite: A comprehensive solution that integrates inventory management with financials.
- Cin7: Focuses on multi-channel retail, providing a wide array of integrations.
Moreover, choosing a cloud-based solution can also provide flexibility, allowing users to manage inventory from anywhere and at any time.
Automation Trends in Warehouse Management
Automation is transforming warehouse management into a finely-tuned machine, and businesses are reaping the rewards. Automated systems reduce manual labor and errors, meaning that goods move in and out of warehouses more smoothly. This leads to improved turnaround times and operational efficiency.
Some notable automation trends include:
- Automated Picking Systems: Robots can pick and pack items, which can be quicker and more accurate than human workers.
- Drones: Some warehouses are employing drones for aerial inventory counts, which can cut down on labor-intensive scanning processes.
- Smart Shelving: This technology can monitor stock levels in real time and alert managers when items need restocking.
Using Data Analytics for Inventory Optimization
Data is like the fuel that powers decision-making in modern inventory management. Utilizing data analytics allows businesses to gain insights into inventory performance, aiding in inventory optimization. By analyzing purchasing patterns, seasonal trends, and demand fluctuations, companies can maintain optimal inventory levels and reduce carrying costs.
Key benefits of employing data analytics in inventory management:
- Forecasting Demand: Accurate projections can result in aligning inventory with actual customer demands.
- Reducing Waste: Understanding which items move quickly prevents overstocking less popular products.
- Improving Supplier Relationships: Data-driven insights help businesses negotiate better with suppliers based on historical trends.
Adapting to these modern technologies not only prepares a business for the future but also positions it as an industry leader capable of meeting demands head-on. Companies not willing to adapt risk becoming fossils in a digital age, where smart operations are the new norm.
Best Practices for Effective Inventory Control
Effective inventory control is the backbone of any thriving business. It is about more than simply keeping track of what’s on your shelves. It encompasses ensuring that you have the right amount of stock at the right time to meet customer demands while minimizing holding costs. Poor inventory control can become a liability, leading to stockouts, overstocking, and ultimately, dissatisfied customers. Therefore, knowing best practices in inventory management is crucial for streamlining processes, boosting productivity, and enhancing overall business performance.
Establishing Inventory KPIs
Key Performance Indicators, or KPIs, serve as essential tools for measuring how well inventory management practices are functioning. It is vital to choose indicators that align with clear business objectives. Common KPIs include inventory turnover ratio, carrying cost of inventory, and order accuracy rate. By closely monitoring these metrics, businesses can identify areas for improvement and make informed decisions.
For instance, if the inventory turnover ratio is low, it could suggest that you are holding too much stock. Conversely, a high turnover rate might point to stockouts, indicating that a reorder strategy needs to be revised. Implementing regular reviews of these KPIs ensures businesses stay on the ball.
Conducting Regular Inventory Audits
Regular inventory audits, whether scheduled or surprise, are pivotal in maintaining accuracy in stock levels. These audits help verify that the physical inventory matches the recorded inventory. Discrepancies can arise for various reasons, including theft, miscounting, or system errors. An audit, therefore, is more than a routine check; it is a tool for financial health and operational reliability.
Using a systematic approach to audits could include cycle counting or full stock counts. Cycle counting involves taking a small subset of inventory and counting it on a specific day, allowing for a more manageable monitoring process. On the other hand, full stock counts involve analyzing all inventory over a designated period. The goal is to catch issues before they escalate, ensuring that inventory records provide a clear picture of stock condition and availability.
Streamlining Reorder Processes
An efficient reorder process can significantly reduce the risk of stockouts while ensuring that excess inventory is not accumulating. One of the most effective ways to streamline ordering is through automation. Inventory management software can automatically trigger reorders based on pre-defined stock levels, taking the human error out of the equation.
Additionally, adopting a just-in-time (JIT) strategy means products are ordered only when needed. This helps in minimizing unnecessary inventory costs and lays down a path to improved cash flow. A careful analysis of lead times from suppliers will also ensure that reorder points are set accurately, keeping stock levels balanced and optimization intact.
"By focusing on best practices in inventory management, businesses can significantly enhance efficiency and profitability."
Thus, embracing best practices in inventory control results in tangible benefits, from improved operational efficiency to lesser holding costs. In the world of inventory management, the combination of data-driven decisions and strategic planning is what allows businesses to thrive amidst fierce competition.
Optimizing Warehouse Operations
To put it plainly, optimizing warehouse operations isn’t just a nice-to-have arrangement; it’s a necessity for thriving in today’s competitive landscape. It’s the backbone that supports efficient inventory management and drives overall business success. Bringing a nuanced approach to warehouse management can create significant efficiencies, ultimately translating into cost reductions and improved customer satisfaction.
When we consider what it means to optimize warehouse operations, several critical elements come to mind. The layout of a warehouse is paramount. An organized layout prompts smoother workflow operations and minimizes unnecessary movement. This can lead to both time and labor savings. Another vital component is the incorporation of lean principles. Lean warehousing allows for reduced waste—be it time, materials, or space—resulting in a sleeker operation.
Key benefits to optimizing these operations include:
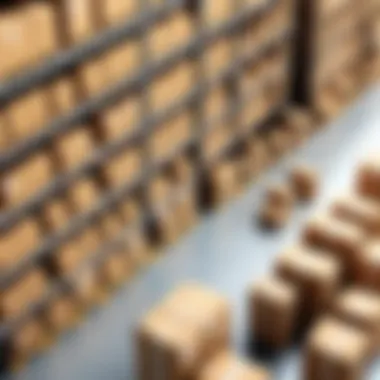
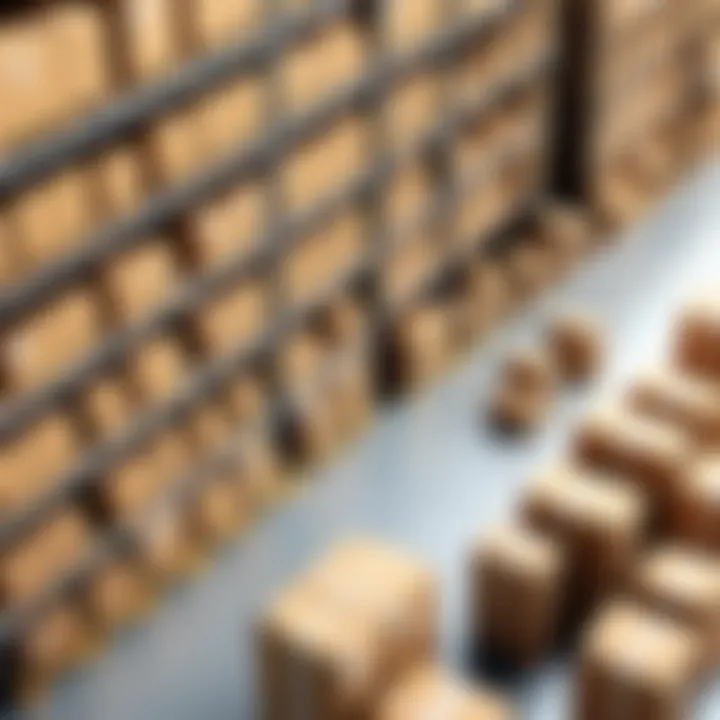
- Enhanced productivity: Employees can access materials swiftly, reducing cycle times.
- Reduced operational costs: Lower labor and inventory carrying costs contribute to a healthier bottom line.
- Improved customer service: A well-organized warehouse means faster order fulfillment, better accuracy, and timely deliveries.
Improving Warehouse Layout for Efficiency
A warehouse layout may seem like a trivial matter, but it can profoundly influence efficiency. The flow of goods and workers must be logical and fluid. Think of it like a dance; if everyone knows the steps, the performance flows beautifully. Employing techniques such as zoning and orderly storage systems can streamline operations. Items should ideally be stored close to where they will be picked, to minimize travel time.
Utilizing technology can further enhance layout efficiency. Deploying automated guided vehicles (AGVs) can help in moving goods without the need for human intervention. Additionally, adopting vertical storage solutions makes the most out of your square footage, creating a more organized and efficient pick path.
Implementing Lean Warehousing Principles
Lean warehousing is about trimming the fat. Imagine your warehouse as a buffet – too much piled on the table can overwhelm. By reducing those excesses—be it through improved inventory management processes or cutting out unnecessary steps—businesses can save time and resources.
To implement lean principles effectively:
- Identify value-added activities: Focus on processes that contribute directly to customer satisfaction.
- Map the value stream: Visual tools can help in identifying waste. Knowing where bottlenecks reside is half the battle won.
- Create a culture of continuous improvement: Encourage staff to provide feedback and suggestions on workflows. Empowered employees often yield powerful insights.
Staff Training and Development
Let's not kid ourselves; a skilled workforce is the lifeblood of any operation, including warehouse management. Without proper training, even the most state-of-the-art systems can flounder. Training doesn’t stop when an employee is hired; staying abreast of new technologies and methods is crucial.
A well-trained team ensures that operational strategies are implemented correctly. Regular workshops focused on safety measures, inventory tracking systems, and equipment use bolster employee confidence and competence.
Moreover, encouraging cross-training can be a boon. It allows for a flexible workforce and ensures there’s always someone available to step in, damaging little to operational flow.
"In today’s fast-paced business environment, keeping your workforce up to speed is not just wise; it’s imperative."
By embedding a culture of continuous learning in warehouse operations, businesses not only optimize efficiency but also pave the way for long-term growth.
The Future of Inventory and Warehouse Management
Understanding the trajectory of inventory and warehouse management in the coming years is not just a passing interest; it is a necessity for any business aiming to thrive in an increasingly competitive landscape. Organizations must keep an eye on advanced trends, technologies, and practices that are reshaping how these functions are carried out. From AI-powered systems to sustainable practices, the future holds a myriad of opportunities that can enhance operation efficiencies, reduce costs, and improve customer satisfaction.
Emerging Trends in the Industry
In a rapidly evolving market, several trends have begun to take root, signaling what lies ahead for inventory and warehouse management.
- Artificial Intelligence and Machine Learning: These technologies are becoming central to the decision-making processes. AI algorithms can analyze historical data to predict inventory needs accurately, thus reducing excess stock and avoiding stockouts.
- Internet of Things (IoT): Devices that communicate in real-time allow businesses to track inventory levels, monitor equipment health, and pinpoint inefficiencies. For example, RFID tags can continuously relay information about the location and condition of stock items.
- Blockchain Technology: A growing number of firms are looking into blockchain for enhancing transparency across the supply chain. This tech can ensure product authenticity and streamline transactions, providing a secure and immutable record.
These trends not only make operations more efficient but also provide strategic insight for long-term planning. Moreover, businesses adept in leveraging these trends can outpace their competition.
Sustainability Practices in Inventory Management
Sustainability in inventory management is not merely a buzzword — it is becoming a fundamental consideration. The growing focus on environmental responsibility is compelling businesses to rethink their practices. Here are some points worth mentioning:
- Optimizing Resource Usage: Techniques such as just-in-time inventory help minimize waste, ensuring that products are manufactured and delivered only as needed.
- Eco-Packaging Solutions: Many firms are shifting to sustainable materials for packaging, which can significantly reduce environmental impact. This move not only appeals to eco-conscious consumers but also can lower shipping costs.
- Circular Economy Models: Implementing systems that promote recycling and repurposing materials can create a more sustainable inventory lifecycle. Companies like IKEA and Unilever are already exploring ways to integrate this approach into their operations.
Adopting these sustainability practices can distinguish a business in a crowded marketplace and resonate with customers who prioritize corporate responsibility.
Important Note: Staying ahead in these areas is no longer optional but a fundamental component of long-term success in inventory and warehouse management.
Integrating these emerging trends and sustainability practices into inventory and warehouse management strategies puts businesses in a better position to adapt to the changing landscape of global commerce. The foreseeable future will demand agility, innovation, and a commitment to responsible practices that align with both market demands and societal expectations.
Closure
In closing, the realm of inventory and warehouse management comes across as more than mere logistics or stock counts; it’s the backbone of efficient operations and customer satisfaction. Companies that grasp the intricacies of these fields can navigate the complexities of supply chains with a precision akin to a well-tuned orchestra, ensuring that every instrument plays its part at the right time.
Summary of Key Insights
Understanding both inventory management and warehouse management paves the way for businesses to harness significant benefits. First, mastering the core principles allows for better organization of resources and improves overall workflow.
Specific insights include:
- Interdependence: Inventory and warehouse systems are not standalone entities; their interplay is critical.
- Technology enhancement: Utilizing modern software solutions can streamline inventory processes and enhance accuracy in stock levels.
- Best practices: It’s about establishing actionable KPIs and audits to ensure that stock levels align with demand.
These insights empower small to medium-sized businesses to sharpen their competitive edge and meet customer demands efficiently.
Next Steps for Businesses
For businesses eager to make strides in their inventory and warehouse management, a set of scalable actions can serve as foundational steps:
- Conduct a Full Review: Evaluate existing inventory practices and warehouse layouts. Identify gaps and inefficiencies.
- Embrace Technology: Explore options in inventory management software and automation tools. Prioritize solutions that can be easily integrated with existing systems.
- Training and Development: Invest in staff training. Employees should be well-equipped to leverage new tools and processes.
- Monitor Performance: Develop a framework for performance measurement. Regular reviews ensure that processes evolve in sync with market changes.
By taking these next steps, businesses not only enhance their operational efficiency but also forge a resilient foundation designed to adapt to the ever-evolving landscape of inventory and warehouse management.