Optimize Tracking Equipment Maintenance Strategies
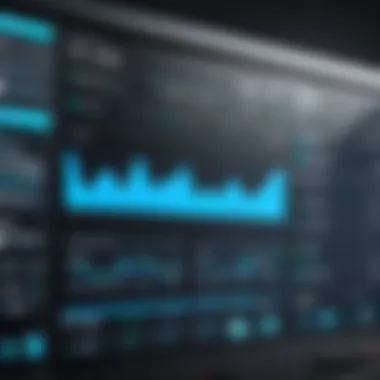
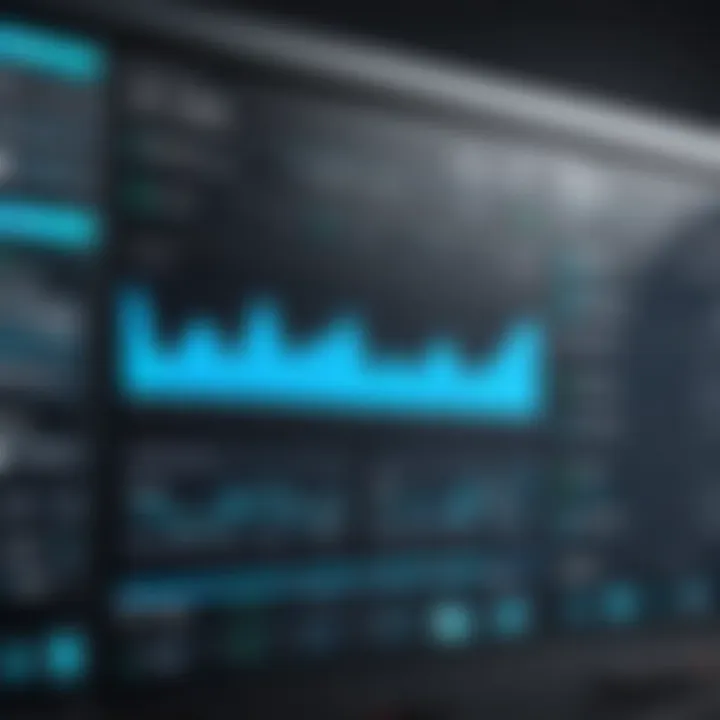
Intro
In today's fast-paced business environment, tracking equipment maintenance is not merely a best practice; it is essential for operational efficiency and cost management. As small to medium-sized business owners and technology decision-makers pursue ways to optimize their operations, the significance of maintaining equipment cannot be overstated. Doing so effectively leads to enhanced performance, reduced downtime, and substantial savings over time.
Failure to track equipment maintenance can result in unexpected breakdowns and costly repairs, which can impede productivity. Therefore, businesses must adopt structured methodologies, utilize advanced technologies, and employ proactive strategies to ensure that their equipment remains in optimal condition throughout its lifecycle. This article serves as a guide to understanding these critical aspects, offering actionable insights into best practices for tracking equipment maintenance.
Overview of Key Features
Essential Software Capabilities
When selecting a tracking equipment maintenance software, it is pivotal to assess its core features. Asset management, for instance, enables organizations to keep detailed records of their equipment, including specifications, service history, and warranty information. Furthermore, effective schedule management is vital, allowing businesses to set reminders for routine maintenance activities based on time, usage, or even environmental conditions.
Another crucial element is report generation. Well-designed software provides the ability to produce reports that analyze equipment performance, maintenance costs, and downtime. This insight can be invaluable for making informed budgetary and operational decisions. Additionally, mobile access is increasingly popular, empowering maintenance teams to log information on the go and access critical data from any location.
Unique Features That Differentiate Options
Different software solutions boast unique offerings that may cater to specific industry needs. While some focus on preventive maintenance strategies, ensuring issues are solved before they escalate, others may provide real-time monitoring capabilities through IoT integration. This level of tracking allows businesses to respond swiftly to performance issues before they affect operational efficiency.
Moreover, integration capabilities with existing systems can be a deciding factor. For example, software that meshes seamlessly with inventory management or enterprise resource planning systems can greatly streamline operations.
User Experience
Interface and Usability
User experience plays a significant role in the adoption of any software. An intuitive interface enhances productivity and encourages user engagement. The software should prioritize a clean design, ensuring essential functions are easily accessible. Well-organized menus and tooltips can facilitate user onboarding and reduce the learning curve for maintenance staff.
Support and Community Resources
In addition to usability, robust support mechanisms are necessary for troubleshooting and maximizing software potential. Whether via comprehensive documentation, responsive customer support, or user communities, access to help can greatly enhance software effectiveness. Engaging in forums or community discussions can also provide insights into best practices and creative solutions from peers in the industry, fostering a collaborative environment.
"Effective tracking of equipment maintenance is not just about repair timelines; it's about ensuring optimal performance and minimizing total lifecycle costs."
Conclusively, acknowledging the importance of well-structured tracking equipment maintenance practices is crucial. Utilizing the right technologies, understanding user needs, and ensuring proper support will lead toward improved operational efficiency and reduced overhead costs.
Understanding the Importance of Equipment Maintenance Tracking
Equipment maintenance tracking is crucial for organizations aiming to optimize their operations. The value of effective maintenance systems is profound. They not only enhance the longevity of the equipment but also significantly impact overall efficiency, costs, and compliance with safety regulations. For businesses, especially small to medium-sized ones, integrating a systematic maintenance tracking approach can be transformative.
Operational Efficiency
Operational efficiency is one of the primary benefits of maintenance tracking. When machinery and equipment are regularly monitored, it minimizes unexpected downtimes caused by failures. Timely maintenance ensures all equipment runs at peak performance. This results in greater production capabilities, reduced cycle times, and enhanced output. Moreover, with the right tracking systems in place, organizations can predict when equipment will require maintenance based on usage data.
Regular checks and maintenance help identify wear and tear before they escalate into larger problems. This proactive approach leads to smoother operations, allowing teams to focus on their core tasks without interruptions from unexpected machinery breakdowns.
Cost Reduction
Cost reduction is a key advantage that cannot be overlooked. A well-maintained system reduces repair costs significantly. This is because preventive maintenance, when properly tracked, often costs less than emergency repairs. Additionally, equipment that is regularly maintained tends to consume less energy and operates more efficiently. This reduction in operational costs can have a noticeable effect on the bottom line.
When organizations commit to maintenance tracking, they can also optimize their inventory costs. With a clear view of maintenance schedules and requirements, they can better manage spare parts and minimize excess inventory. Thus, proper management leads to decreased overhead costs in the long run.
Compliance and Safety
Compliance with industry regulations is another imperative aspect. Many sectors have stringent guidelines regarding equipment maintenance and safety standards. By accurately tracking maintenance schedules, organizations can ensure they meet all necessary legal requirements. This not only fosters a culture of safety but also protects the business from potential fines and legal issues.
Effective maintenance tracking is also associated with improved safety standards. Well-maintained equipment poses less risk to employees. Ensuring machinery is in optimal condition minimizes accidents and injuries. Thus, a company not only safeguards its workforce but also maintains its reputation and operational integrity.
Regularly tracking equipment maintenance saves time and resources, ensuring compliance while prioritizing safety.
Key Components of an Effective Maintenance Tracking System
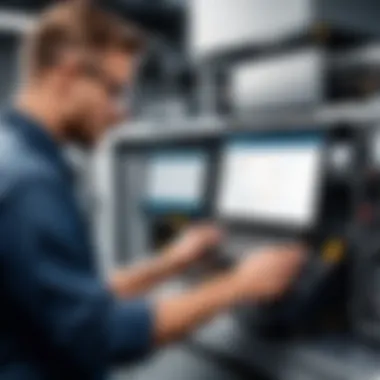
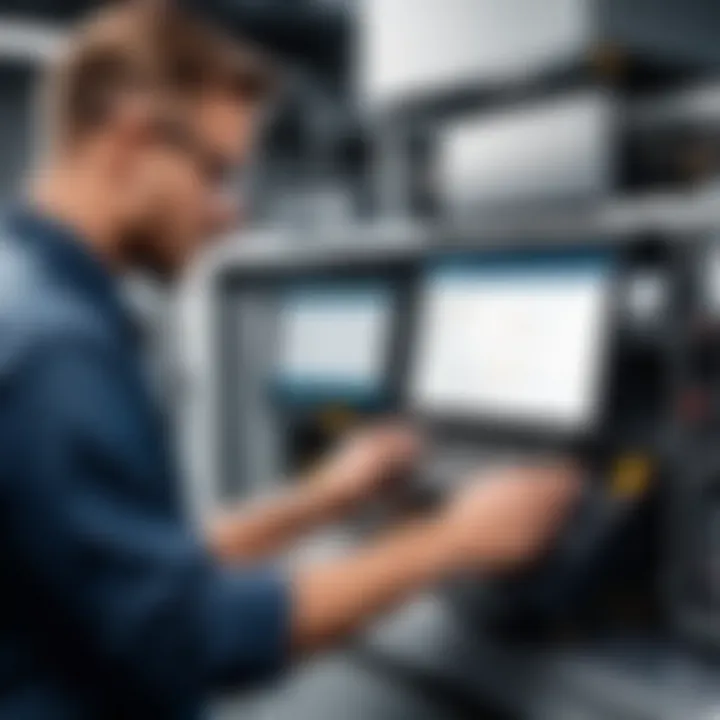
An effective maintenance tracking system is essential for ensuring operational efficiency and minimizing costs. Understanding the importance of its key components is crucial for organizations aiming to improve equipment performance and reliability. The right system helps in managing not only the maintenance schedules but also the inventory and data collection methods.
Maintenance Schedule
A maintenance schedule is fundamental to any equipment tracking system. It outlines what maintenance needs to be performed and when. This proactive approach prevents unexpected equipment failures and downtime. By having a clear schedule, businesses can prioritize tasks and allocate resources effectively.
For example, implementing a calendar system for routine inspections can help teams stay organized. Technologies such as Computerized Maintenance Management Systems (CMMS) can automate these schedules, sending reminders when maintenance is due. Regular tasks may include oil changes, filter replacements, and safety checks. By adhering to the maintenance schedule, businesses can enhance equipment durability and reliability.
Inventory Management
Maintaining an adequate inventory of spare parts and tools is another vital component. Efficient inventory management minimizes downtime that can result from waiting for parts. Techniques such as Just-In-Time (JIT) can be beneficial. JIT ensures that parts are available only when needed, reducing storage costs and waste.
Using barcoding or RFID technology can greatly improve inventory organization and tracking. By systematically logging each part's usage and reorder levels, businesses can maintain optimal inventory levels. This discipline ensures that equipment is kept running smoothly, further supporting operational efficiencies.
Data Collection Methods
Data collection is the backbone of any maintenance tracking system. The insights gained from properly collected data can inform decision-making processes. Regularly logging maintenance activities, equipment performance, and failure rates provides a wealth of information. It helps identify trends and predict when equipment may require more intensive maintenance.
Different methods exist for data collection, including manual logging, automated systems, or mobile applications. Each method has its strengths. For instance, mobile applications allow for real-time data entry, which can be advantageous in the field. Proper data collection enables organizations to evaluate the effectiveness of their maintenance strategies and make informed adjustments.
"A well-structured data collection method can spell the difference between routine maintenance and strategic asset management."
In summary, an effective maintenance tracking system relies on a solid schedule, efficient inventory management, and robust data collection methods. These components work together to enhance equipment lifespan and ensure operational continuity.
Technologies Supporting Equipment Maintenance Tracking
The advent of advanced technologies reshapes the landscape of equipment maintenance tracking. These technologies streamline processes, enhance data accuracy, and provide valuable insights. Applying them can help organizations boost efficiency and reduce costs. It is vital to explore how they contribute to a strong maintenance strategy.
CMMS Software
Computerized Maintenance Management System (CMMS) software stands as a cornerstone of modern maintenance practices. This tool centralizes maintenance data, enabling teams to manage tasks effectively. With features such as automated scheduling and work order tracking, CMMS software helps reduce downtime significantly.
Key benefits of CMMS include:
- Enhanced Reporting: Generate detailed reports on equipment performance, maintenance history, and costs.
- Preventive Maintenance: Schedule routine checks based on data-driven insights, reducing the likelihood of unexpected failures.
- User-Friendly Interfaces: Provide training opportunities for staff, facilitating easier adoption of the system.
Selecting the right CMMS is critical. Factors to consider include scalability, integration capabilities, and vendor support. Ultimately, an effective CMMS can transform maintenance operations, leading to improved asset lifespan and reliability.
Mobile Applications
Mobile applications have emerged as powerful tools for maintenance tracking. They offer the flexibility to access maintenance data on the go. Technicians can update work orders, retrieve manuals, and log completed tasks from any location. This immediacy boosts productivity and improves communication among team members.
Benefits of using mobile maintenance apps include:
- Real-Time Communication: Teams can share updates instantly, reducing delays.
- User Accessibility: Technicians can access information directly at the equipment site, increasing accuracy in maintenance tasks.
- Customizable Alerts: Set notifications for scheduled maintenance, ensuring timeliness in upkeep.
As organizations pursue mobile solutions, choosing applications that easily integrate with existing CMMS platforms is important. This synergy ensures a seamless flow of information across all systems.
IoT and Smart Equipment
The Internet of Things (IoT) has revolutionized maintenance strategies. Smart equipment can now communicate their own maintenance needs, offering real-time data to prevent breakdowns. This proactive approach allows businesses to respond quickly to maintenance requirements, leading to increased operational efficiency.
Consider the benefits of IoT in maintenance tracking:
- Predictive Analysis: Use data analytics to predict potential equipment failures before they occur, enabling timely interventions.
- Remote Monitoring: Allows continuous tracking of equipment health without the need for on-site inspections.
- Cost-Effective Solutions: Reduces manual labor and minimizes unplanned downtime, saving companies money.
Employing IoT technology entails some challenges, such as ensuring data security and managing network connectivity. Nevertheless, the long-term returns justify the initial investments.
Overall, integrating these technologies creates a more resilient and efficient maintenance tracking process, directly influencing a business's bottom line.
Integrating Maintenance Tracking into Business Processes
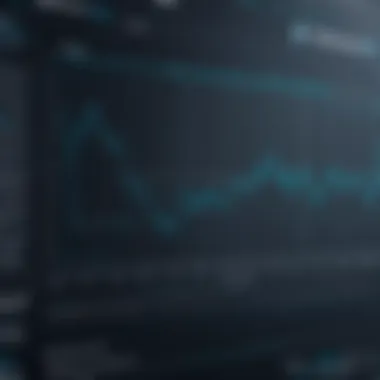
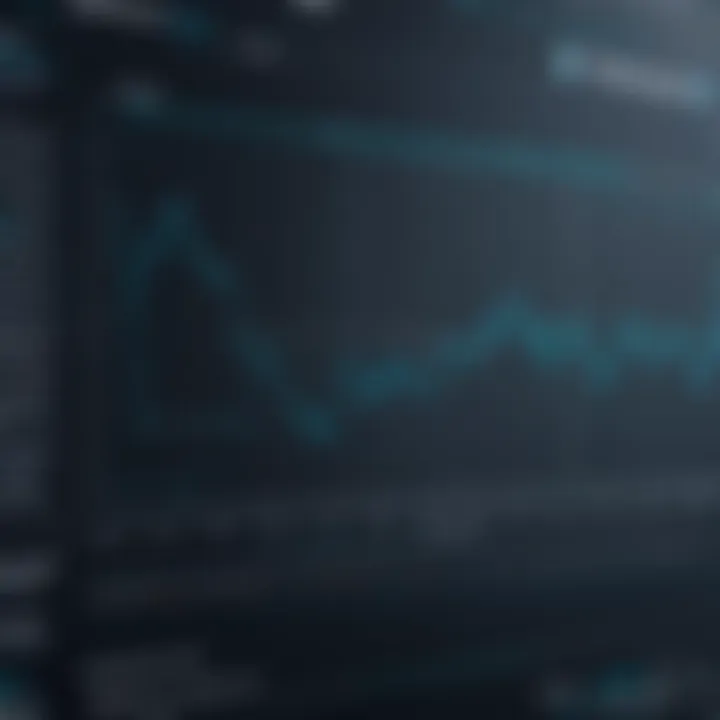
Integrating maintenance tracking into business processes is crucial for any organization that relies on equipment. This integration ensures that maintenance activities are not standalone tasks but part of a larger operational strategy. The key elements to focus on include workflow understanding, collaboration among team members, and establishing feedback loops. Each of these aspects brings unique benefits that enhance overall equipment reliability and performance.
Understanding Workflow
A clear understanding of workflow is essential. Workflow refers to the sequence of processes through which a piece of work passes. In maintenance tracking, knowing how maintenance tasks fit into the overall production or service delivery system can significantly enhance efficiency. Companies should map out their workflows to identify critical pathways where maintenance activities can be integrated seamlessly.
Doing so allows for scheduling maintenance during downtimes or low-impact times to prevent disruptions. Consider documenting key steps in the workflow and assessing where maintenance tasks align with them. The better integrated these tasks are, the less likely they are to interfere with operational productivity.
Collaborating with Team Members
Collaboration is another important factor. When team members across different departments communicate effectively, it boosts the efficiency of maintenance tracking. Regular meetings and communication ensure that everyone understands their roles regarding equipment maintenance. This also promotes a culture of transparency, where every team member contributes insights that can enhance maintenance practices.
To facilitate collaboration, creating cross-functional teams that include members from operations, maintenance, and management can be valuable. By pooling knowledge and sharing feedback, teams can address equipment issues more proactively and increase equipment uptime. Moreover, using digital tools and applications for tracking can streamline this collaboration, making it easier for team members to access and share relevant information.
Feedback Loops
Finally, creating effective feedback loops is vital for refining maintenance processes over time. Feedback loops are systems that allow for continuous assessment and improvement. When maintenance tracking integrates with operational frameworks, teams can collect feedback on equipment performance after maintenance actions. This feedback can inform whether maintenance practices are effective or if they require adjustments.
Establish mechanisms to regularly review performance metrics to assess maintenance effectiveness. For example, if the Mean Time Between Failures (MTBF) declines, it may indicate a need for changes in maintenance strategies. Developing an open culture where team members feel comfortable sharing their observations and suggestions is critical in fostering an environment of continuous improvement.
"Incorporating maintenance tracking within established business processes leads to smarter operations and better use of resources."
Integrating maintenance tracking into business processes yields several benefits. It optimizes workflows, enhances collaboration, and drives ongoing improvements. Such an integrated approach allows businesses to maximize equipment uptime, reduce costs, and ensure compliance with safety regulations.
Challenges in Equipment Maintenance Tracking
In the realm of equipment maintenance, tracking involves numerous hurdles that businesses must navigate. These challenges can hinder the effectiveness of maintenance practices and impact overall operational efficiency. Understanding these difficulties is crucial for devising strategies that streamline the process. Here, we will examine the prominent challengesโdata overload, resource allocation, and resistance to change.
Data Overload
Data overload occurs when organizations collect excessive information without a structured system for processing it. In equipment maintenance tracking, this can lead to confusion and inefficiencies. Technological advancements have enabled businesses to gather vast amounts of data from their equipment, such as operational metrics, maintenance logs, and usage patterns. However, without proper management protocols and analytical tools, this data can become a burden rather than a benefit.
- Businesses need to prioritize what data is essential for decision-making.
- Utilizing data visualization tools can help in interpreting complex datasets clearly.
- Implementing a data filtering mechanism can assist in focusing on relevant information, ultimately improving reaction times and maintenance effectiveness.
Resource Allocation
Effective allocation of resources is essential for implementing a successful maintenance tracking system. It involves not just financial resources but human capital as well. Companies must ensure they have the right tools and personnel in place to support maintenance activities. A common issue arises when organizations fail to accurately assess their existing resources, leading to either underutilization or overallocation.
- Identifying skill gaps within the team is imperative. Proper training can enhance the team's ability to manage maintenance tasks efficiently.
- Investing in the right technology, such as computerized maintenance management systems (CMMS), can optimize resource management.
- Regular reviews of resource allocation strategies can lead to better decisions and improved system performance.
Resistance to Change
Resistance to change is a well-known challenge that affects any effort to implement new practices. When businesses attempt to overhaul their maintenance tracking processes, employees may hesitate to adopt new systems or workflows. This reaction often stems from a lack of understanding or fear of the unknown.
- Clear communication about the benefits of the new tracking systems can help alleviate fears.
- Involving staff in the decision-making process fosters a sense of ownership and may reduce ambivalence towards new practices.
- Continuous support and training can ease the transition, making it more likely for employees to embrace change.
"Successfully overcoming challenges in equipment maintenance tracking leads to improved efficiency and cost savings, ultimately fostering long-term growth and stability."
Metrics and KPIs for Tracking Maintenance Effectiveness
Tracking maintenance effectively requires a clear framework of metrics and key performance indicators (KPIs). These measurements provide tangible evidence of how well equipment is being maintained and can help identify areas needing improvement. The significance of metrics lies in their ability to drive informed decisions, maximize uptime, and optimize operational resources. In various industries, these KPIs can serve as benchmarks to analyze performance trends and to implement data-driven strategies aimed at enhancing equipment reliability.
Mean Time Between Failures (MTBF)
Mean Time Between Failures (MTBF) is a critical metric that indicates the average time between failures of a system. It essentially measures the operational reliability of equipment. Calculating MTBF involves dividing the total operating time by the number of failures during that time. A higher MTBF is usually a positive indicator, suggesting that equipment is running smoothly with fewer operational disruptions.
MTBF can be a strong predictor for maintenance scheduling. By understanding the average time until a failure occurs, businesses can anticipate when maintenance should be performed proactively rather than reactively. This can save significant time and resources, as unplanned downtime often incurs higher costs due to emergency repairs and production delays.
Scheduled vs. Unscheduled Maintenance Ratio
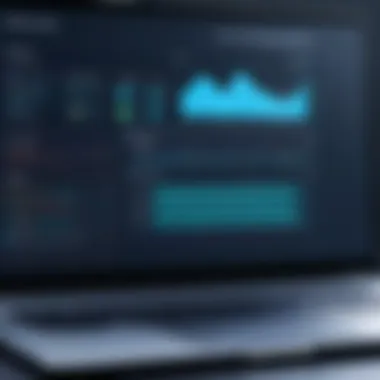
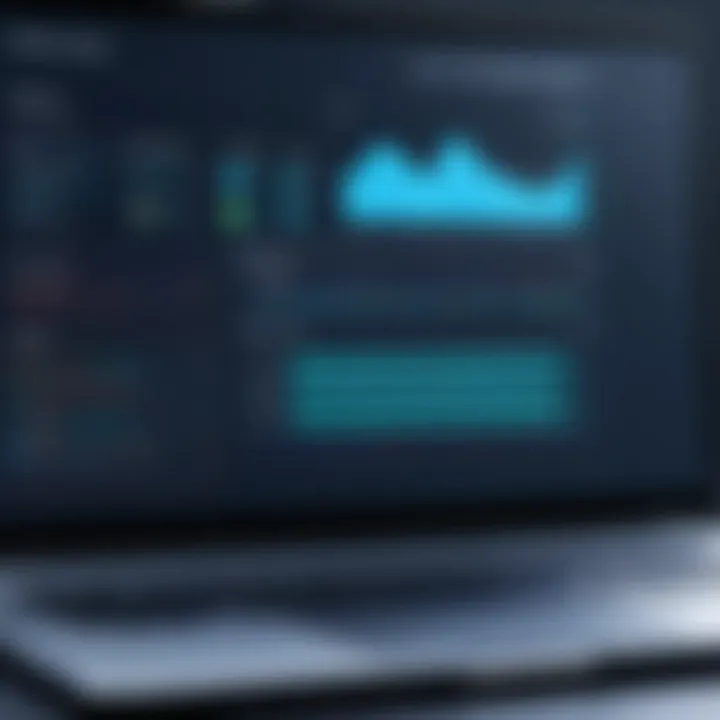
Analyzing the Scheduled vs. Unscheduled Maintenance Ratio is essential for gauging maintenance effectiveness. This ratio compares how much maintenance work is planned versus how much repairs occur unexpectedly. A high proportion of unscheduled maintenance may indicate underlying issues such as inadequate predictive maintenance strategies or equipment that is nearing the end of its lifecycle.
Businesses generally strive for an optimal ratio where scheduled maintenance predominates, as it indicates proper maintenance planning and execution. Conversely, a high rate of unscheduled maintenance can lead to increased operational costs and reduced equipment lifespan. Regular reviews of this ratio help organizations prioritize preventive measures over reactive fixes, thus improving overall asset management.
Maintenance Cost as a Percentage of Asset Value
Maintenance Cost as a Percentage of Asset Value is another invaluable metric. It expresses maintenance expenditure relative to the current value of the assets being maintained. Understanding this percentage helps businesses assess whether their maintenance costs are sustainable compared to the value of the equipment.
Tracking this metric over time allows organizations to identify trends in spending and to make adjustments to their maintenance strategies. Higher maintenance costs relative to asset value can signal issues, such as aging equipment or inefficient practices. Conversely, keeping this percentage low while maintaining high operational reliability is an indicator of effective asset management.
Best Practices for Equipment Maintenance Tracking
Best practices in equipment maintenance tracking serve as a cornerstone for ensuring your assets remain reliable and efficient. Effective tracking is not just a formality; it fundamentally influences operational workflows, cost efficiency, and the lifespan of equipment. Focusing on specific practices enhances overall productivity. It is crucial to embed these practices into the organizational culture to reap long-term benefits.
Regular Audits
Conducting regular audits is essential in spotting discrepancies in maintenance practices. Audits can help verify that all equipment items are operating optimally and that maintenance schedules are adhered to.
The process usually involves examining:
- Asset Condition: Check if any equipment is showing signs of wear or if repairs are needed.
- Maintenance History: Review logs to ensure that routine checks are being done as scheduled.
- Compliance: Validate that all maintenance practices align with industry regulations.
Regular audits go beyond merely ticking off boxes; they nurture a culture of accountability. They can also identify areas for improvement in your maintenance strategy, leading to better resource allocation.
Training Staff
Training staff is pivotal in employing best practices for equipment maintenance. Proper training ensures that employees are aware of procedures and the significance of meticulous tracking. It helps reduce errors in logging data and enhances safety protocols.
Key aspects of staff training include:
- Best Practices: Focus on teaching the importance of proper equipment use and maintenance protocols.
- Software Tools: Familiarize staff with maintenance tracking systems like CMMS for accurate data entry and retrieval.
- Safety Training: Incorporate safety measures to minimize accidents that can occur during maintenance.
Investing time and resources into comprehensive training can yield substantial dividends in operational safety and equipment reliability.
Documentation Standards
Maintaining clear documentation standards is crucial in conveying essential information about equipment maintenance. Documentation should be precise, consistent, and accessible. Established standards help ensure all personnel interpret maintenance logs uniformly.
Consider the following key elements of robust documentation practices:
- Standard Operating Procedures (SOPs): Ensure SOPs are readily available and followed rigorously.
- Audit Trails: Create detailed logs that capture every maintenance action taken, allowing for easy reviews during audits.
- Templates: Utilize standardized templates for reporting maintenance activities to streamline data processing and minimize errors.
Clear and concise documentation lays the groundwork for effective communication, transparency, and informed decision-making within the organization.
The End
The conclusion is a pivotal section that encapsulates the essence of tracking equipment maintenance. It distills essential information, ensuring that the reader is aware of key learnings and the practical implications of what has been discussed throughout the article. Understanding the importance of this topic helps to reinforce the necessity of investing time and resources into an effective maintenance tracking system.
Effective tracking not only improves operational efficiency but also leads to significant cost reduction. Businesses that prioritize maintenance tracking can extend the life of their equipment, ultimately saving money in the long run. Moreover, compliance with safety regulations becomes easier with proper tracking, reducing the risk of accidents and legal issues.
Beyond these aspects, it is crucial for business leaders to recognize that tracking maintenance is an evolving process. The integration of modern technology with traditional methods can yield substantial benefits. Data-driven decisions, coupled with a proactive approach, can transform how maintenance is perceived within an organization, shifting it from being a cumbersome task to an integral part of the overall business strategy.
Recap of Key Insights
The key insights drawn from this discussion can be succinctly summarized as follows:
- Operational Efficiency: A well-structured maintenance tracking system enhances workflow and minimizes downtime.
- Cost Management: Preventive maintenance reduces unscheduled repairs and operational costs.
- Safety and Compliance: Keeping accurate records supports adherence to safety standards and promotes a safer work environment.
- Technological Integration: Leveraging tools such as CMMS software, mobile applications, and IoT technology streamline processes.
In essence, effective equipment maintenance tracking is not just a financial or operational concern; it is a vital strategic advantage that can differentiate a business in a competitive landscape.
Calls to Action
To fully realize the benefits of effective equipment maintenance tracking, stakeholders should take the following actions:
- Evaluate Current Practices: Take time to assess existing maintenance protocols. Identify gaps that need addressing and opportunities for improvement.
- Invest in Technology: Explore software solutions like Fiix or MaintainX that streamline tracking and reporting. Assess which tools align with your operational needs.
- Develop a Maintenance Culture: Encourage a culture that values maintenance among employees. Training and awareness can lead to better compliance and proactive engagement.
- Set Clear Goals and Metrics: Establish KPIs related to maintenance effectiveness, such as MTBF or maintenance costs as a percentage of asset value, to measure progress over time.
By actively implementing these strategies, organizations can enhance their equipment maintenance efforts, reaping both immediate and long-term rewards.