Understanding Centralized Maintenance Management Systems
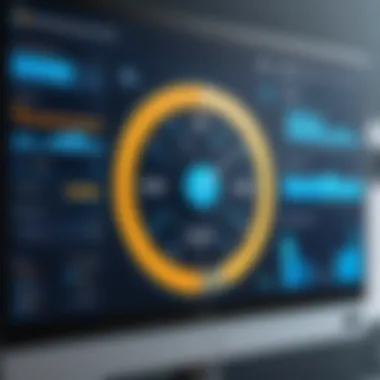
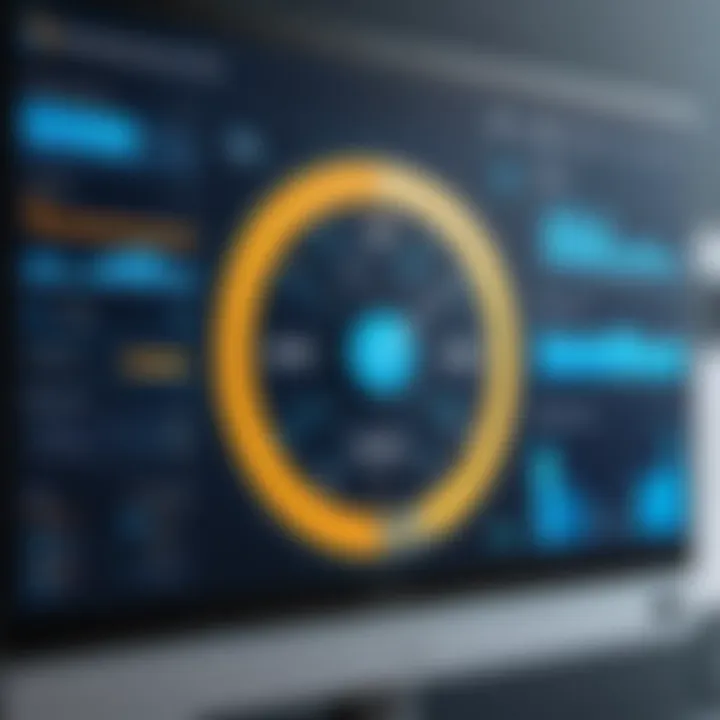
Intro
Centralized Maintenance Management Systems (CMMS) play a critical role in modern business operations. Companies often find themselves facing increasing demands for efficiency, cost management, and operational effectiveness. In this context, a CMMS emerges as a powerful tool, enabling organizations to streamline maintenance processes, enhance productivity, and boost overall performance.
The central idea behind these systems is to manage maintenance activities from a unified platform. This not only simplifies coordination but also ensures that everyone involved has access to the same information and resources. This article will examine the essential features, user experiences, and challenges of implementing a CMMS.
Overview of Key Features
Essential Software Capabilities
A robust CMMS typically encompasses several essential capabilities:
- Asset Management: It allows organizations to monitor their assets, track maintenance history, and schedule preventive maintenance.
- Work Order Management: This feature streamlines the process of creating, assigning, and tracking work orders, reducing downtime and ensuring timely maintenance interventions.
- Inventory Management: A CMMS helps manage and track spare parts and materials, minimizing stockouts and excess inventory costs.
- Reporting and Analytics: Valuable insights can be gained from data with built-in reporting tools. This is crucial for decision-making and strategy development.
- Mobile Access: Web-based or mobile-enabled platforms permit technicians to access and update tasks in real time, promoting timely maintenance responses.
Unique Features that Differentiate Options
Different CMMS solutions have distinct features that set them apart:
- Integration Capabilities: Some systems offer extensive APIs for integration with other business tools and software like ERP systems for seamless data flow.
- Customizability: The ability to tailor workflows, dashboards, and reports according to the specific needs of an organization.
- User Roles and Permissions: Fine-grained control over user roles can optimize security and management.
"The functionalities of a CMMS can significantly vary among options, influencing not only user experience but also bottom-line results."
User Experience
Interface and Usability
User experience is a significant factor for adoption success. A CMMS should have a clean, intuitive interface that promotes ease of use. Key aspects to consider include:
- Navigation: The system should allow users to move across different functionalities effortlessly.
- Customization Options: Customizable dashboards can help users focus on the metrics that matter most to them, enhancing productivity.
Support and Community Resources
Access to quality support and an active user community can play a crucial role in the overall experience of using CMMS. Potential users should evaluate:
- Documentation: Well-structured and easily accessible documentation can significantly reduce learning curves.
- Online Forums: Active forums or community sites can provide additional help and share best practices.
- Vendor Support: Consider the availability of technical support from the vendor, including response times and resources for troubleshooting.
Intro to Centralized Maintenance Management Systems
In the realm of business operations, efficiency and organization stand as pillars of success. This article focuses on centralized maintenance management systems (CMMS) which are crucial for optimizing maintenance processes. With increasing complexity in operations across various industries, implementing a robust CMMS offers substantial benefits. These systems assist organizations in maintaining a holistic view of their assets, ensuring timely maintenance while reducing downtime and unexpected failures.
Understanding CMMS
Centralized maintenance management systems are software solutions designed to centralize the management of maintenance activities. They enable organizations to track work orders, schedule preventive maintenance, and manage inventory all from one interface. By seamlessly integrating these tasks, CMMS helps in reducing the manual effort involved in these operations.
Key features typical of a CMMS include:
- Work Order Management: Automates the process of creating, tracking, and closing work orders.
- Asset Tracking: Keeps detailed records of equipment and machinery, including location, age, and maintenance history.
- Preventive Maintenance Scheduling: Facilitates the setting up of maintenance schedules based on time intervals or usage metrics.
- Inventory Management: Oversees spare parts and supplies to ensure that essential components are available when needed.
Clearly, CMMS plays a significant role in enhancing maintenance efficiency.
Historical Context
The evolution of centralized maintenance management has been shaped by technological advancements and organizational needs. Initially, maintenance management relied heavily on paper-based systems or basic spreadsheet functions. These methods were prone to errors and inefficiencies, leading to operational challenges. Over time, the demand for reliability and improved performance prompted the development of specialized software.
The first CMMS solutions emerged in the 1980s, focusing on automating routine tasks and providing easier access to maintenance data. As technology progressed, CMMS systems continued to evolve, incorporating features like mobile access, cloud solutions, and data analytics. Today’s CMMS offerings are highly sophisticated, enabling organizations to adopt more strategic approaches to maintenance management.
Implementing a CMMS in this day and age not only aligns with market demands but also ensures that businesses remain competitive. The historical context highlights how these systems have matured to meet complex operational needs.
The Need for Centralized Maintenance Management
Centralized Maintenance Management Systems (CMMS) are not just tools; they are critical frameworks for organizations today. The ongoing evolution of market dynamics and technology requires businesses to reassess their maintenance strategies. A centralized approach to maintenance management streamlines operations, enhances efficiency, and reduces costs, making it an indispensable asset in an increasingly competitive landscape.
Market Trends and Challenges
The marketplace is witnessing a shift towards more integrated operational models. Increasing reliance on technology has created a demand for sophisticated and centralized maintenance management systems. As businesses face constant pressure to maximize productivity and minimize downtime, CMMS emerged as the solution to several existing challenges.
Organizations must adapt to various trends, including:
- Increasing Automation: With more machinery relying on automated systems, the need for advanced maintenance solutions has matured.
- Data-Driven Decision Making: Companies are now focusing on data analytics to inform maintenance schedules and identify issues before they escalate.
- Regulatory Compliance: As regulations around safety and environmental impact sharpen, businesses require systems that can maintain accurate records and ensure compliance.
However, challenges persist. The process of selecting a suitable CMMS can be daunting. Many businesses dread the initial investment and the potential for integration hiccups. It is common for organizations to struggle with resistance to change from employees used to traditional processes.
Key Issues in Maintenance Management
In any maintenance management strategy, several key issues must be addressed:
- Resource Allocation: Effectively managing labor and materials is essential for maximizing efficiency. Many organizations face hurdles in balancing available resources with the demand for maintenance tasks.
- Training and User Adoption: A top-notch CMMS means little if employees are not proficient in its use. Providing adequate training is vital for success.
- Integration Issues: Existing systems may lack compatibility with new CMMS solutions, leading to data silos and fragmented workflows. Businesses must prioritize seamless integration to unlock the full potential of these systems.
- Performance Monitoring: Without clear metrics and performance indicators, measuring the success of a maintenance strategy becomes challenging.
The shift towards centralized maintenance management is not just a trend; it's a necessity for organizations aiming to thrive in a competitive environment.
By recognizing these pressing issues, organizations can better prepare themselves for the transition to a CMMS. This proactive approach ensures that they not only adopt new technologies but also integrate them efficiently and effectively into their existing operations.
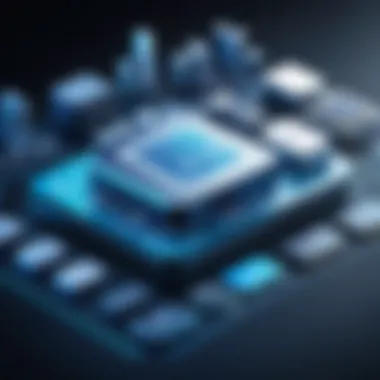
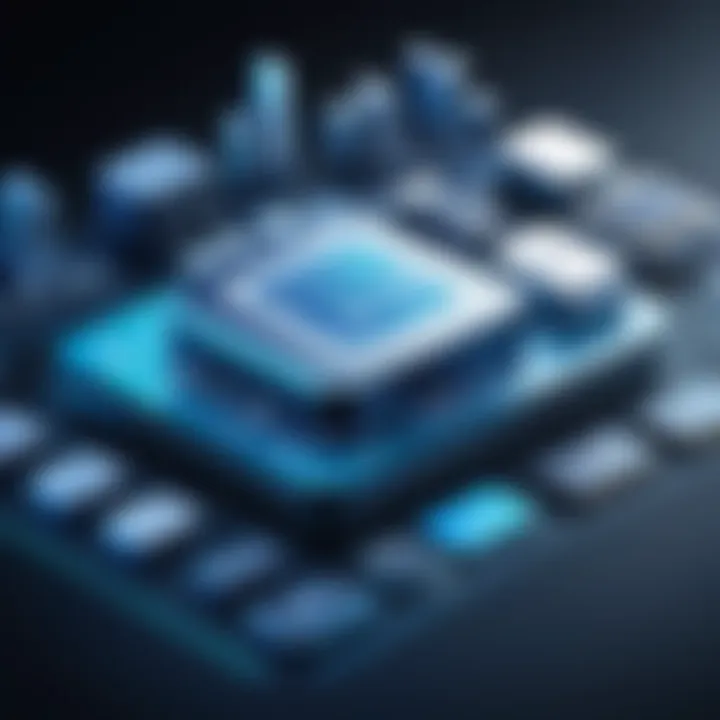
Core Features of CMMS
Centralized maintenance management systems (CMMS) are built to enhance operational effectiveness. Understanding their core features is crucial for any organization aiming to optimize maintenance workflows. Key functionalities not only streamline tasks but also provide strategic advantages that can influence the overall performance of an organization. Here are the main features that should be examined:
Work Order Management
Work order management is a pillar of any effective CMMS. This feature allows for the creation, assignment, and tracking of work orders seamlessly. Users can log issues and request maintenance with a few clicks. This reduces the time spent on manual processes and improves response times. Efficient work order management also ensures tasks are prioritized correctly, which is vital in maintaining equipment reliability.
Key aspects include:
- Automated notifications for technicians when new assignments are made.
- Tracking capabilities that allow managers to monitor progress in real time.
- Simplification of complex processes which leads to quicker resolution of maintenance issues.
Asset Tracking
Asset tracking functions provide a comprehensive view of all organization assets. Knowing where each asset is located and its current status is essential for effective maintenance management. This feature helps reduce downtime by ensuring that all necessary resources are available when needed. Tracking systems may include:
- Identification via barcodes or RFID tags.
- Recording of asset history, such as repairs and upgrades.
- Insights into asset performance, leading to more informed decision-making.
Preventive Maintenance Scheduling
Preventive maintenance scheduling is crucial for prolonging the life of equipment. This feature allows organizations to automate routine maintenance tasks before issues arise. By scheduling maintenance activities, companies can avoid unplanned downtimes and costly repairs. The essential benefits include:
- Enhanced reliability of equipment which supports higher productivity.
- Cost savings through avoidance of emergency repairs.
- Better resource planning as it helps allocate technical staff effectively.
Inventory Management
Inventory management within a CMMS focuses on keeping optimal stock levels of maintenance parts and supplies. This feature eases the procurement process while ensuring that essential items are always on hand. An effective inventory system offers:
- Real-time visibility of stock levels.
- Alerts for low inventory to avoid delays in maintenance.
- Streamlined ordering processes to maintain adequate supplies without excessive expenditure.
A CMMS must have these core features to truly embody its purpose of enhancing maintenance operations. By integrating these functionalities, businesses can expect considerable improvements in operational efficiency, reduced costs, and enhanced performance.
Benefits of Centralized Maintenance Management Systems
Centralized Maintenance Management Systems (CMMS) play a crucial role in modern business operations. Their significance lies in the quantifiable advantages they offer, which not only bolster efficiency but also slashes operational costs. Understanding the benefits of CMMS is essential for organizations aiming to enhance reliability and maintenance practices.
Increased Operational Efficiency
One of the primary benefits of a CMMS is the marked increase in operational efficiency. By centralizing maintenance activities, businesses can streamline processes that were once dispersed and disorganized. A CMMS facilitates real-time tracking of work orders, asset status, and resource allocation. Consequently, technicians can prioritize tasks better and reduce time lost in miscommunication or data searching. This leads to smoother workflow and improved overall productivity.
In addition, preventive maintenance becomes easier with a CMMS. Scheduled maintenance routines, configured within the system, minimize the chances of unexpected breakdowns. As machines operate more reliably, there is less disruption to production schedules. The impact on efficiency becomes evident in metrics such as increased uptime and decreased operational bottlenecks.
Cost Reduction Strategies
Implementing a CMMS enables organizations to adopt various cost reduction strategies. One significant area of savings comes from minimizing equipment downtime. By proactively managing maintenance, firms can avoid costly repairs and lost productivity caused by equipment failures. Depending on the industry, amounts saved can be significant.
Moreover, a focused CMMS can optimize parts inventory. It prompts organizations to assess their inventory levels and procurement strategies. This kind of visibility leads to fewer excess parts, reduces carrying costs, and improves cash flow.
Here are a few cost reduction functions of a CMMS:
- Budget Management: Track maintenance spending with real-time data.
- Preventive Maintenance: Reduce the need for costly emergency services.
- Asset Lifespan: Extend equipment life through regular upkeep.
Improved Data Analysis and Reporting
An often-overlooked benefit of a CMMS is its capability for enhanced data analysis and reporting. With all maintenance data centralized, businesses can analyze historical data to identify trends that require attention. For instance, recurring issues with certain machinery can prompt an in-depth review of operational processes.
Additionally, customized reporting can reveal valuable insights. Organizations can assess their maintenance programs' effectiveness and make evidence-based decisions moving forward. Such reports support continuous improvement, a core tenet of successful maintenance strategies.
"By leveraging CMMS for data reporting, companies can shift from reactive to proactive decision making, significantly enhancing their competitive edge."
In summary, the benefits of Centralized Maintenance Management Systems are far-reaching. Enhanced operational efficiency, strategic cost reduction, and superior data capabilities make CMMS an invaluable asset for any organization. Businesses must recognize these advantages and consider their application in their maintenance protocols.
Challenges in Implementing CMMS
Implementing a Centralized Maintenance Management System (CMMS) is a multifaceted endeavor that goes beyond simply installing software. Understanding the challenges faced during this process is crucial for businesses aiming to reap the benefits of such systems. Recognizing these challenges allows organizations to anticipate issues and take proactive steps to address them.
Resistance to Change
One of the primary obstacles in adopting a CMMS is resistance to change from employees. This resistance often stems from a variety of factors. Workers may feel apprehensive about new technology or fear that their roles will be altered or diminished. Moreover, if individuals have been accustomed to a particular way of working for a long time, introducing a new system can create discomfort. A thoughtful approach to manage this shift is essential.
- Involve Employees Early: Involve team members in the decision-making process around the CMMS selection. This inclusion helps to foster a sense of ownership and commitment.
- Effective Communication: It’s vital to communicate the benefits of the new system, not just for the organization, but also for individual roles. This helps employees understand how the system will make their jobs easier.
By addressing these areas, organizations can reduce resistance and promote a smoother transition to a CMMS.
Resource Allocation
Another significant challenge is resource allocation during the implementation phase. Implementing a CMMS requires both time and financial investment. Businesses need to carefully consider how to allocate human and financial resources during the transition.
- Budgeting: Developing a clear budget that includes software purchase, training, and ongoing maintenance costs is critical. Unanticipated expenses can derail the project.
- Personnel Training: Adequate attention must also be paid to training staff. Without proper training, even the most advanced systems fail to deliver their promised benefits.
Balancing these resources effectively can lead to a more successful implementation and a higher return on investment.
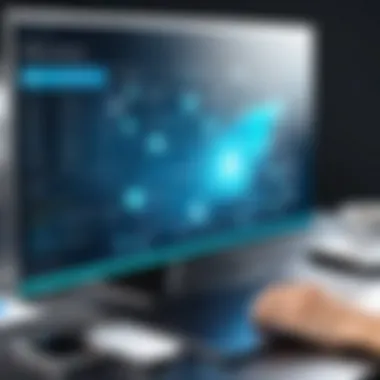
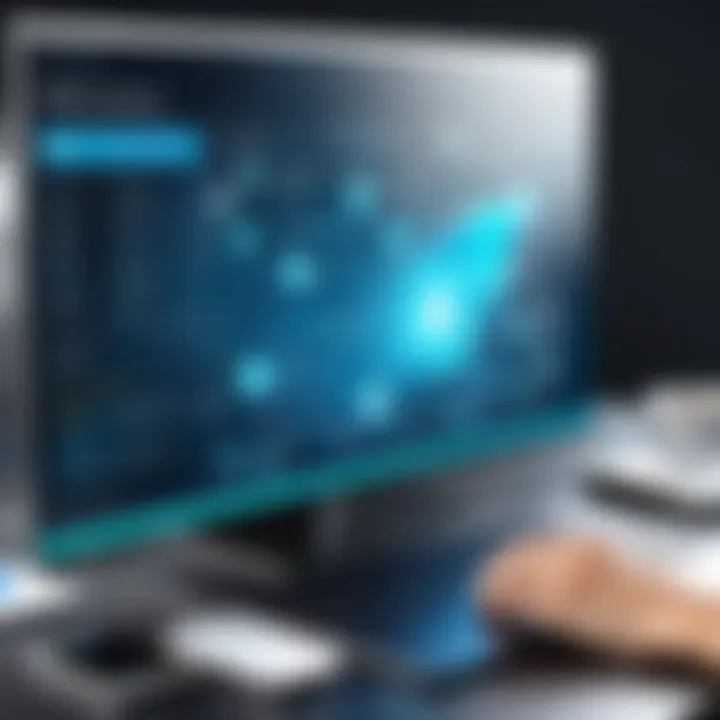
Integration with Existing Systems
Integrating the newly implemented CMMS with existing systems presents yet another layer of complexity. Interoperability issues can lead to data silos, which hinder the system’s effectiveness. For many organizations, legacy systems are deeply entrenched in daily operations, and bypassing these systems is often not an option.
- Assess Existing Infrastructure: Before implementing a CMMS, a comprehensive assessment of current systems should be undertaken to identify potential integration challenges.
- Choose Compatible Solutions: When evaluating CMMS options, consider their compatibility with existing tools. Working with vendors who can offer integration support is also advantageous.
Choosing the Right CMMS Solution
Choosing the right Centralized Maintenance Management System (CMMS) is crucial for organizations aiming to streamline their maintenance operations. A well-suited CMMS offers tailored functionalities that align with specific operational needs. The decision can significantly impact efficiency, safety, and overall productivity. By selecting the most appropriate software, businesses can optimize their resources, reduce downtime, and enhance maintenance reliability.
Evaluating Software Options
When evaluating CMMS software options, it is essential to assess various key features. First, identify which functionalities are vital for your organization. This can vary depending on the nature of your assets and specific maintenance demands. Look for features like work order management, asset tracking, preventive maintenance, and inventory control. Each of these elements plays a critical role in how effective a CMMS will be for your operations.
Moreover, consider user interface and experience. A system may have advanced features but could be difficult to navigate. A user-friendly interface minimizes training time and promotes adoption among employees.
Additionally, check for scalability. As your organization grows, your chosen CMMS should be able to grow with it. Rigidity in the software can stifle ongoing improvement.
Assessing Vendor Support
Vendor support is another crucial factor when selecting a CMMS. Look for a vendor that offers robust technical support, including training resources, documentation, and a responsive customer service team. Support availability can be a game-changer during implementation and usage. If issues arise, having the right support helps reduce downtime and keeps operations running smoothly.
It’s also wise to investigate customer testimonials and case studies to understand the level of support in real-world situations. Look for ratings on vendor reliability and responsiveness. If possible, reach out to existing customers to gain insights about their experiences.
Budget Considerations
Budget is often a significant consideration when choosing a CMMS. Determine both the initial investment and the ongoing costs associated with the software. Look beyond the sticker price; factor in additional costs such as implementation, training, and maintenance fees.
Create a budget that allows for unexpected expenses. It's beneficial to prepare for potential upgrades in the future. Tools evolve, and organizations must plan for software growth.
Prioritize your needs versus wants when budgeting for a CMMS. While it is tempting to choose the most feature-rich option, focus on what will bring the most value to your operations.
Implementation Process of a CMMS
Implementing a Centralized Maintenance Management System (CMMS) is a critical step for any organization aiming to enhance operational efficiency. This process involves a strategic approach to ensure that the system is successfully integrated into the existing operations. It influences how maintenance activities are conducted and how resources are managed. Understanding this process is essential because its success determines the effectiveness of the CMMS in addressing the organization's maintenance needs.
Project Planning
Effective project planning is the cornerstone of a successful CMMS implementation. This phase encompasses defining the goals, objectives, and scope of the CMMS project. It is vital to engage all key stakeholders during this planning stage. Everyone from maintenance teams to IT departments should provide input.
Here are some important steps in project planning:
- Define Objectives: Clearly outline what the organization aims to achieve with the CMMS, such as reducing downtime or improving resource allocation.
- Assess Current Systems: Review current maintenance practices and systems to identify gaps and areas for improvement.
- Allocate Resources: Determine the budget required and the personnel assigned to the project.
- Develop a Timeline: Create a realistic timeline that incorporates phases of the implementation process.
A well-structured project plan can help mitigate risks and manage resources more effectively. It sets the foundation for the entire implementation process.
User Training and Onboarding
Once the project is planned, user training and onboarding become essential. The success of a CMMS substantially hinges on how well users adapt to the new system. Despite the technical features being advanced, if the users do not understand the system, it may not yield the expected benefits.
Effective training should include:
- Hands-on Workshops: Conduct hands-on sessions where users can engage with the system directly, enhancing their familiarity.
- Comprehensive Documentation: Provide thorough user manuals and guides to assist users in navigating the system.
- Support Systems: Set up a support mechanism for users to reach out for help after implementation. This can include online forums or direct contacts.
Engaging users during the training phase can lead to increased satisfaction and less resistance to the new system. This creates a smoother transition into using the CMMS effectively in their daily tasks.
Monitoring and Evaluation
After the CMMS is up and running, ongoing monitoring and evaluation are crucial. This phase ensures that the system meets its stated objectives and adapts to changing needs over time.
Key aspects to monitor include:
- Performance Metrics: Set up key performance indicators (KPIs) that align with the organization’s objectives. Common KPIs include equipment downtime, maintenance costs, and response time to work orders.
- User Feedback: Actively seek user feedback to understand how the CMMS is working in practice. This can be done through surveys or regular check-ins.
- System Updates: Regularly review and update the CMMS to incorporate new features or address any issues that may arise.
Monitoring ensures the CMMS remains relevant and continues to serve the organization's needs. Continuous evaluation offers insights that help refine and enhance maintenance management practices.
Implementing a CMMS is not just about technology; it’s also about aligning processes and people to achieve optimal efficiency.
Comparative Analysis of Popular CMMS Solutions
Centralized Maintenance Management Systems (CMMS) are an essential tool for organizations focused on optimizing maintenance operations. To navigate the crowded market of CMMS solutions, it is crucial to conduct a detailed comparative analysis. This process not only highlights the unique features of various systems but also sheds light on their specific benefits and potential downsides.
The importance of this comparative analysis lies in empowering decision makers with the information needed to choose the right CMMS that would best meet their organizational requirements. As the landscape of maintenance management becomes increasingly sophisticated, selecting the wrong solution can lead to wasted resources, increased downtime, and inadequate data management. Thus, understanding the nuances of different solutions becomes imperative for successful implementation and long-term benefits.
Feature Set Comparisons
When analyzing various CMMS solutions, feature set comparisons are a fundamental factor. Organizations should evaluate critical aspects such as:
- User Interface: An intuitive interface can greatly enhance software adoption. If the software is complicated to navigate, user training may increase.
- Customization Options: Flexibility in customizing the system to fit specific organizational needs is vital.
- Mobile Accessibility: In today’s working environment, mobile access allows staff to manage tasks on the go, increasing efficiency.
- Integration Capabilities: The ability to sync with existing software is essential for a cohesive operational framework.
- Reporting Tools: Robust reporting functionalities help in analyzing data trends for proactive decision-making.
By evaluating these features across different systems, organizations can identify which CMMS aligns best with their operational goals and budget constraints.
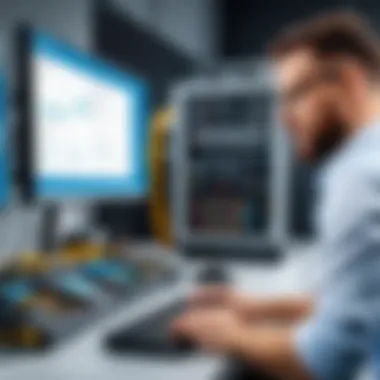
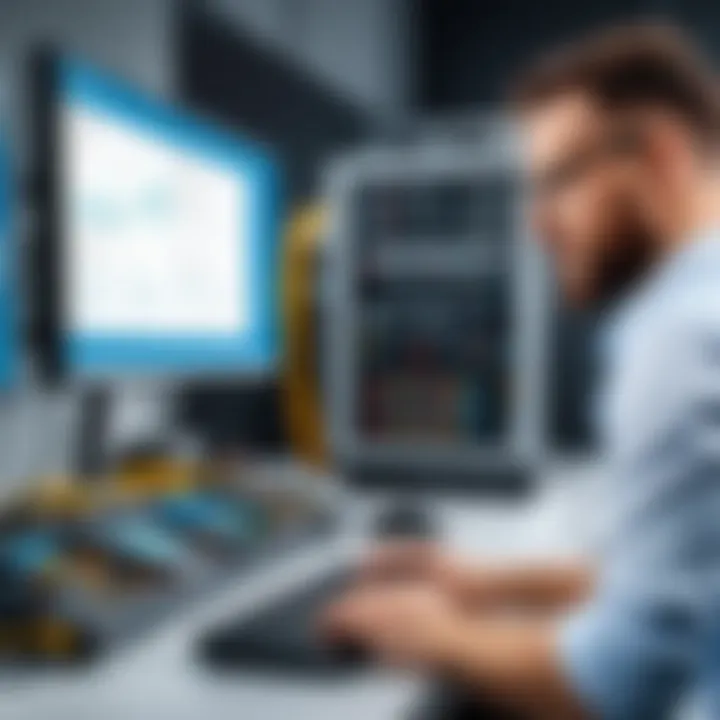
User Feedback and Reviews
User feedback plays a critical role in the comparative analysis of CMMS solutions. Real-world experiences offer insights into usability and efficiency that marketing materials may not fully disclose. Considerations include:
- Ease of Use: User reviews often indicate how straightforward the system is for daily operations.
- Support and Maintenance: Various solutions may come with different levels of customer support. Positive feedback regarding support can signal reliability.
- Performance and Reliability: Consistent performance is paramount in a maintenance management system. Reviews can highlight performance issues that users faced.
- Return on Investment: Users often discuss the financial benefits they have experienced since implementing the CMMS. Understanding practical costs versus the actual benefits received can inform purchasing decisions.
"User feedback and reviews can reveal the underlying strengths and weaknesses of a CMMS solution, which might not be apparent during a trial period."
Though methodologies for collecting feedback vary, online forums such as Reddit and professional social networks can provide valuable perspectives from industry experts. By synthesizing user experiences with feature sets, organizations can make a well-informed decision in selecting the right CMMS.
Future Trends in Maintenance Management
The landscape of maintenance management is evolving rapidly, driven by technological advancements and changing business needs. Understanding these trends is crucial for organizations aiming to stay competitive and optimize their operations. As businesses navigate the complexities of maintenance, they are increasingly looking towards future trends to enhance their Centralized Maintenance Management Systems (CMMS).
Integration of IoT
The Internet of Things (IoT) plays a pivotal role in modernizing maintenance management. By connecting devices and equipment through the internet, organizations gain real-time insights into asset performance and health. This integration allows for predictive maintenance, where potential issues can be identified before they escalate into costly failures. For example, smart sensors can detect anomalies in machinery operation and send alerts, enabling timely intervention.
The benefits of IoT integration are manifold:
- Real-time Data Access: Continuous monitoring of equipment conditions.
- Enhanced Decision-Making: Data-driven insights for better maintenance planning.
- Reduced Downtime: Quick identification of faults minimizes operational interruptions.
- Cost Efficiency: Predictive maintenance leads to significant cost savings.
However, adopting IoT also brings certain considerations. Organizations must prioritize data security, as the increased connectivity raises the risk of cyber threats. Additionally, proper training for staff is necessary to interpret and act on the data generated by IoT devices effectively.
Artificial Intelligence Applications
Artificial Intelligence (AI) is another trend reshaping maintenance management. AI algorithms can analyze vast amounts of data to identify patterns and predict equipment failures. By leveraging machine learning techniques, systems can continuously improve their predictions based on historical data.
Some applications of AI in maintenance management include:
- Failure Prediction: Identifying potential failures before they occur.
- Resource Optimization: Allocating resources more efficiently based on predictive analytics.
- Automated Work Orders: Triggering maintenance requests automatically when anomalies are detected.
The incorporation of AI not only amplifies efficiency but also enhances reliability in maintenance operations. However, integrating AI solutions requires a thoughtful approach, considering compatibility with existing systems and addressing the need for quality data input. In summary, both IoT and AI integration are crucial for shaping the future of maintenance management. Doing so effectively positions organizations to achieve operational excellence.
Case Studies of Successful CMMS Implementation
The real-world implementation of Centralized Maintenance Management Systems (CMMS) highlights their transformative potential. Case studies provide concrete evidence of how organizations can leverage these systems to overcome challenges in maintenance management. This section reviews significant industry-specific applications of CMMS and assesses the return on investment (ROI) for various companies.
Industry-Specific Applications
Different industries exhibit unique maintenance requirements, allowing CMMS to showcase versatility. For instance, in manufacturing, CMMS plays a crucial role in scheduling preventive maintenance, thus reducing equipment downtime. Take Ford Motor Company, for example. They adopted a sophisticated CMMS that integrated real-time data, allowing them to analyze equipment performance efficiently. As a result, they reported a 20% reduction in machine breakdowns over the first year of implementation.
In healthcare, organizations like the Mayo Clinic have utilized CMMS to streamline asset management, ensuring that critical medical equipment is always operational. By investing in a tailored CMMS, they improved their compliance with regulatory standards. The system also enhanced their ability to track maintenance history, which is vital in medical settings where equipment failure can have severe consequences.
On the other hand, the hospitality industry, including chains like Marriott, have employed CMMS to improve guest experiences. By maintaining facilities effectively, they could minimize service disruptions. Implementing a CMMS enabled these chains to adopt preventive maintenance schedules that align with off-peak times, thus ensuring that the customer experience remains seamless.
"Case studies elucidate the real benefits and adaptability of CMMS across various sectors, making a compelling case for their adoption."
ROI Analysis and Impact Assessment
Assessing the ROI of a CMMS is essential for understanding its value. Every investment requires a careful examination of costs versus benefits. A comprehensive ROI analysis not only justifies the expenditure but also highlights potential savings and efficiency gains.
In the manufacturing sector, businesses often measure ROI through increased productivity and reduced downtime. For instance, a study indicated that companies implementing CMMS could achieve a return of $3 for every $1 invested over a five-year period. Metrics like reduced labor hours, decreased repair costs, and extended asset lifespan contribute to this positive ROI.
In healthcare, ROI can be evaluated through improved patient care and equipment reliability. One hospital reported a 15% increase in operational efficiency after implementing CMMS, translating to cost savings in both maintenance and operational expenditures.
Additionally, in the facility management sector, organizations have noted that a robust CMMS reduces paperwork and manual processes significantly. This efficiency translates to labor cost savings. In one case, a facility management company reduced administrative tasks by 40% after adopting a CMMS, illustrating significant potential for cost savings.
The End and Recommendations
In the realm of centralized maintenance management systems (CMMS), understanding the conclusion and recommendations is essential for organizations aiming to enhance their maintenance operations. This section synthesizes the insights derived from previous discussions, emphasizing the significance of committing to a CMMS and the long-term benefits it can provide.
The adoption of a CMMS can lead to numerous positive outcomes. Improved visibility into operations allows for better resource allocation. As businesses gather data, they can analyze trends that inform decisions. Moreover, it reduces the likelihood of unexpected equipment failures, therefore conserving resources and maintaining productivity.
There are specific elements to consider when concluding your exploration of CMMS. First, the importance of actively engaging end-users cannot be overstated. Their feedback will drive further enhancements in the system. Second, organizations should conduct regular audits and assessments of their CMMS to ensure alignment with evolving business needs and technological advancements. This approach ensures the system remains relevant.
Key Benefits of Implementing CMMS:
- Enhanced tracking of maintenance tasks and equipment usage
- Streamlined communication among team members
- Increased data accuracy for informed decision-making
- Reduction in operational costs due to better management of resources
Overall, the successful integration of a CMMS demands careful planning, adaptation, and continuous improvement. Organizations must approach their CMMS journey with a mindset geared toward learning and evolution. The recommendations provided earlier in the article should guide decision-makers in their approach to adopting new technologies.
"Embracing a CMMS is not just an investment in technology but a commitment to a culture of excellence and continuous improvement."
By prioritizing user engagement and remaining attuned to the system's performance, organizations set the foundation for ongoing success. This transformational journey begins with the right mindset and dedication to enhancing maintenance practices.
Final Thoughts on CMMS
As we wrap up this exploration, it is important to synthesize the core philosophy behind CMMS. The essence of a CMMS goes beyond just software or tools; it is about cultivating an organizational culture that values efficient maintenance operations. The ongoing dialogue about maintenance management needs to include key stakeholders from different levels within the organization. Communication ensures that the system is utilized to its full potential and adapts to any changes in operations or market demands.
Best Practices for Continuous Improvement
Continuous improvement in CMMS involves systematic evaluation and adjustments. Here are best practices to integrate:
- Regular Training: Conduct sessions to keep users informed on new functionalities and best practices.
- Solicit Feedback: Encourage users to provide feedback regularly. Their experiences can guide necessary updates or modifications.
- Benchmark Performance: Compare maintenance performance against industry standards to identify areas for improvement.
- Maintain Documentation: Ensure documentation of processes and policies is up-to-date. This clarity can streamline onboarding and ease transitions during system changes.
- Leverage Analytics: Utilize data analytics within the CMMS to track performance and drive decision-making. It transforms raw data into actionable insights.
By recognizing that CMMS is an evolving entity, organizations can harness its full potential and maximize its impact on their maintenance strategies. Adopting these practices lays the groundwork for a robust and responsive maintenance environment.